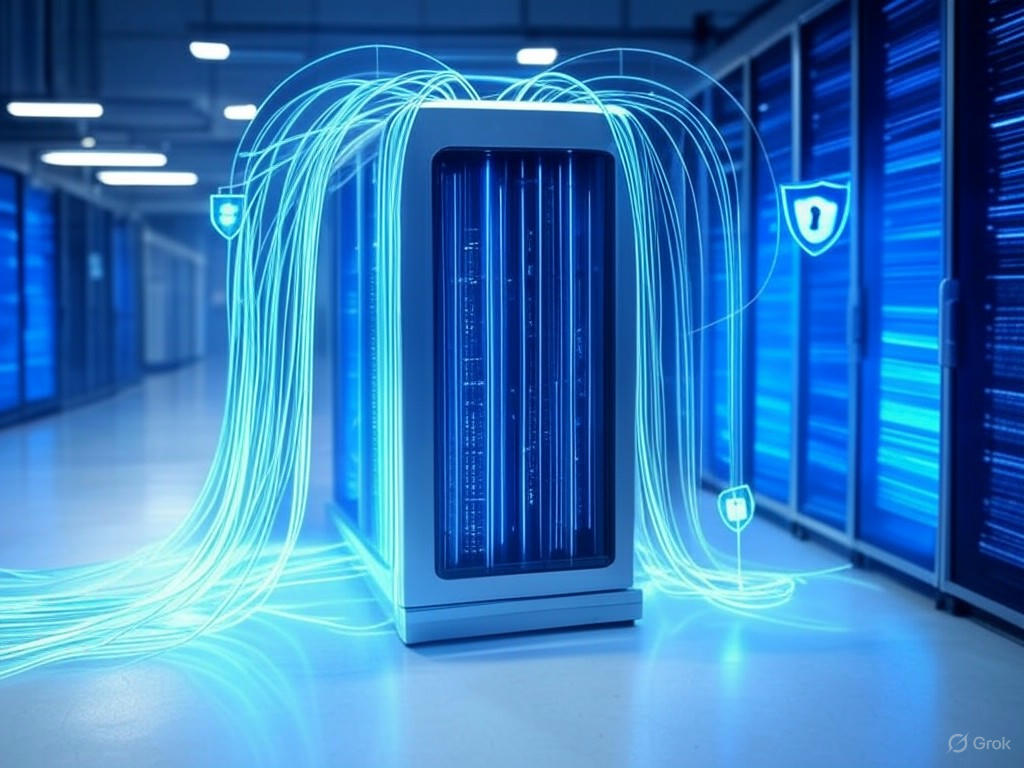
Choosing the Best Industrial IoT Gateway: Connectivity & Security Guide
- Introduction: Why Industrial IoT Gateway Selection Matters—Beyond the Spec Sheet
- Industrial IoT Gateways: The Linchpin Between OT and IT
- The Real-World Stakes: Downtime, Security, and Performance
- Why Evidence and Real-World Fit Matter More Than Marketing Claims
- What This Article Will Cover—and How
- Connectivity Fundamentals: Protocol Support, Interoperability, and Real-World Integration
- Wired and Wireless Connectivity: Reliability vs. Flexibility in the Real World
- Protocol Translation: The Hidden Bottleneck
- Interoperability with Mixed-Vintage Machinery: Bridging Brownfield and Greenfield
- Supporting Both Legacy and Modern Standards: Future-Proofing Your Deployment
- Bottom Line: Test, Don’t Assume—And Prioritize Evidence Over Claims
- Security: Hardware, Firmware, and Network Protections in Practice
- Hardware-Based Protections: More Than a Spec Sheet
- Firmware and Network Protections: Defending the Data Pipeline
- Comparing Security Postures Across Leading Models
- Deployment Longevity, Compliance, and Risk: Security Choices with Lasting Impact
- Best Practices: Practical Recommendations
- Performance and Reliability: Edge Computing, Environmental Hardening, and Operational Metrics
- Introduction
- Edge Processing: Real-World Compute Where It Matters
- Environmental Hardening: Spec Sheets vs. Deployment Reality
- Operational Performance: Throughput, Sensor Read Rates, and Uptime
- Remote Device Management and Failure/Recovery in the Field
- Limitations and Innovations: An Evidence-Based Perspective
- Comparative Analysis and Future Outlook: Benchmarking Top Gateways and Emerging Trends
- Connectivity: Protocol Breadth Is Table Stakes—Integration Quality Sets Winners Apart
- Security: Progress, but Persistent Gaps—Operational Integration Is the Real Test
- Reliability: Ruggedization, MTBF, and the True Cost of Downtime
- Protocol Support: Interoperability and Ecosystem Realities
- Emerging Trends: What’s Next—and What Actually Matters for Long-Term Buyers
- Practical Guidance for Buyers
- Bottom Line
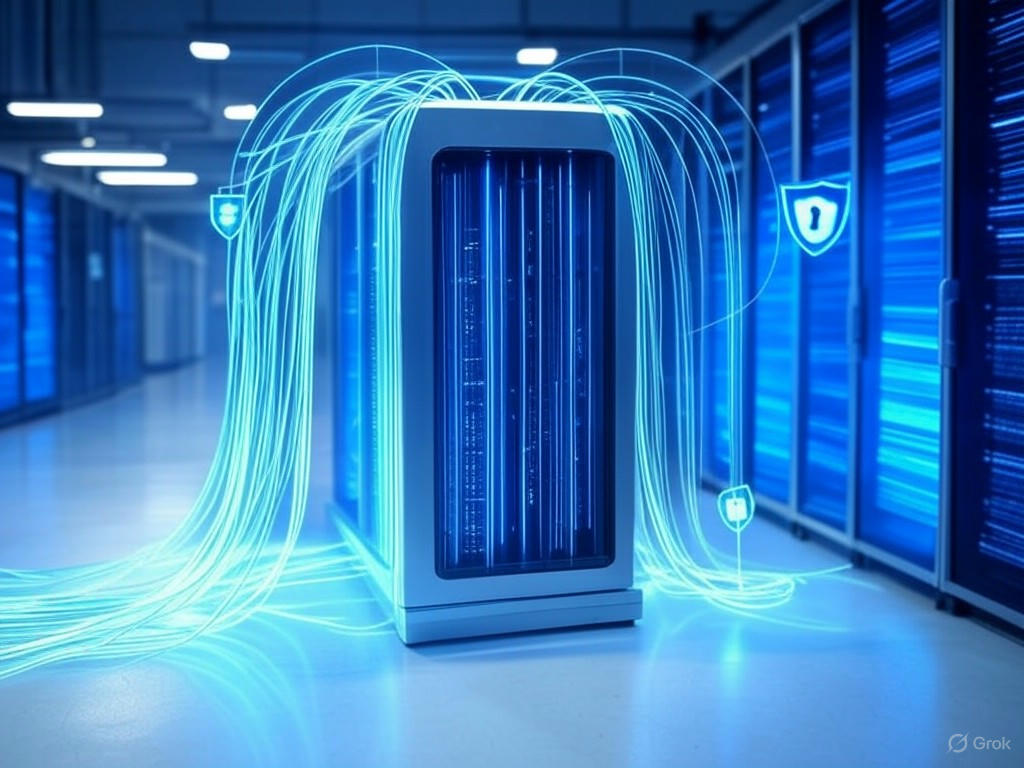
Introduction: Why Industrial IoT Gateway Selection Matters—Beyond the Spec Sheet
Selecting the Right Industrial IoT Gateway
Selecting the right industrial IoT gateway isn’t a matter of chasing the newest processor or the highest throughput on a spec sheet. The real question is: can this device reliably bridge your operational technology (OT)—the machinery, sensors, and controls on your plant floor—with your information technology (IT) systems, all while standing up to the daily punishment of industrial environments? Too often, decision-makers get lost in technical jargon and overlook how these devices directly impact uptime, security, and the bottom line.
Industrial IoT Gateways: The Linchpin Between OT and IT
Let’s clarify what an industrial IoT gateway actually is. Think of it as the central nervous system for your connected operations. It sits between legacy PLCs, modern sensors, and IT/cloud infrastructure—translating protocols, aggregating data, and enforcing security at the intersection of physical machinery and digital analytics. Gateways aren’t just routers or data pipes; they’re intelligent intermediaries, often with edge computing capabilities. By processing data close to its source, gateways cut latency and network congestion, enabling real-time decisions even in bandwidth-constrained or remote sites.
The industrial context raises the stakes. Gateways must wrangle a zoo of protocols (OPC UA, Modbus RTU/TCP, MQTT, DH+, and more), support ruggedized hardware that can survive heat, dust, vibration, and moisture, and increasingly provide onboard AI or machine learning for predictive maintenance and anomaly detection. As the number of connected industrial devices surges past 18 billion globally (IoT Analytics), the need for robust, scalable, and secure gateways has never been greater.
The Real-World Stakes: Downtime, Security, and Performance
Misjudging a gateway purchase isn’t a minor oversight—it’s a risk with six- or seven-figure implications. Downtime in heavy industry averages $125,000 per hour, with some organizations reporting losses above $1 million per hour. A gateway that fails due to overheating, intermittent connectivity, or protocol translation errors can halt production or leave critical assets unmonitored. Conversely, a well-matched gateway can enable predictive maintenance, which has been shown to reduce unplanned downtime by up to 45% and save hundreds of thousands of dollars per incident (McKinsey).
Security is equally critical. Industrial IoT gateways are prime targets for ransomware groups and advanced persistent threat (APT) actors because they bridge isolated OT assets and the broader IT network. Over 80% of organizations have reported an IoT-related security breach, often stemming from poorly secured gateways or outdated firmware. Unlike consumer IoT, a single breach here can mean loss of production data, compromised safety systems, or even full operational stoppages—problems that extend far beyond a typical IT incident.
Why Evidence and Real-World Fit Matter More Than Marketing Claims
Marketing materials love to tout “AI-ready” or “secure by design.” In reality, most failures happen when the gateway doesn’t match the deployment environment or operational workflow. For example, a device rated for -10°C to 50°C will not survive in an oil field where temperatures fluctuate from -40°C to +60°C (see Fatbox G3, TEKTELIC gateways). Likewise, a gateway with only Wi-Fi and cellular connectivity will falter in a steel mill plagued by electromagnetic interference—where redundant wired links are essential.
Practical selection means digging into real deployment data, not just vendor promises. Will the gateway hold up against prolonged vibration or high humidity? Can it maintain secure, low-latency data flows with hundreds of legacy and next-gen devices on a unified platform? Reliable performance comes from field-tested evidence (like Red Lion FlexEdge’s <100ms protocol bridging latency or OnLogic’s 70% reduction in dust-related failures), comparable deployments, and a clear understanding of operational constraints—not the flashiest datasheet.
What This Article Will Cover—and How
If you’re looking for a shopping list of model numbers, you’re in the wrong place. Instead, this article will break down what actually matters when selecting an industrial IoT gateway for your use case—starting with connectivity and security, the two pillars of reliable, scalable industrial IoT. Drawing on real-world deployments and critical metrics (supported protocol stacks, edge compute capacity, hardware hardening, compliance standards), we’ll highlight both genuine innovations and real limitations.
You’ll get actionable, user-focused insights: what questions to ask, what pitfalls to avoid, and how to weigh performance data against operational realities. The goal is to arm you with the tools to make an informed, evidence-based choice—one that supports your operations today and scales for tomorrow. In industrial IoT, the right gateway isn’t just a box on the network; it’s the linchpin for uptime, security, and operational efficiency.
Criteria | Importance in Industrial IoT Gateways |
---|---|
OT-IT Bridging | Ensures reliable communication between machinery/sensors (OT) and IT/cloud systems |
Protocol Support | Handles diverse protocols (OPC UA, Modbus, MQTT, etc.) for legacy and modern devices |
Ruggedization | Withstands harsh industrial environments (heat, dust, vibration, moisture) |
Edge Computing | Processes data locally, reduces latency, enables real-time decision-making |
Security | Protects against cyber threats; critical as gateways bridge OT and IT networks |
Uptime & Reliability | Minimizes downtime, maintains production continuity, supports predictive maintenance |
Connectivity Options | Offers redundant and robust connectivity (wired, wireless, cellular) |
Deployment Fit | Matches real-world operational requirements, not just marketing specs |
Connectivity Fundamentals: Protocol Support, Interoperability, and Real-World Integration
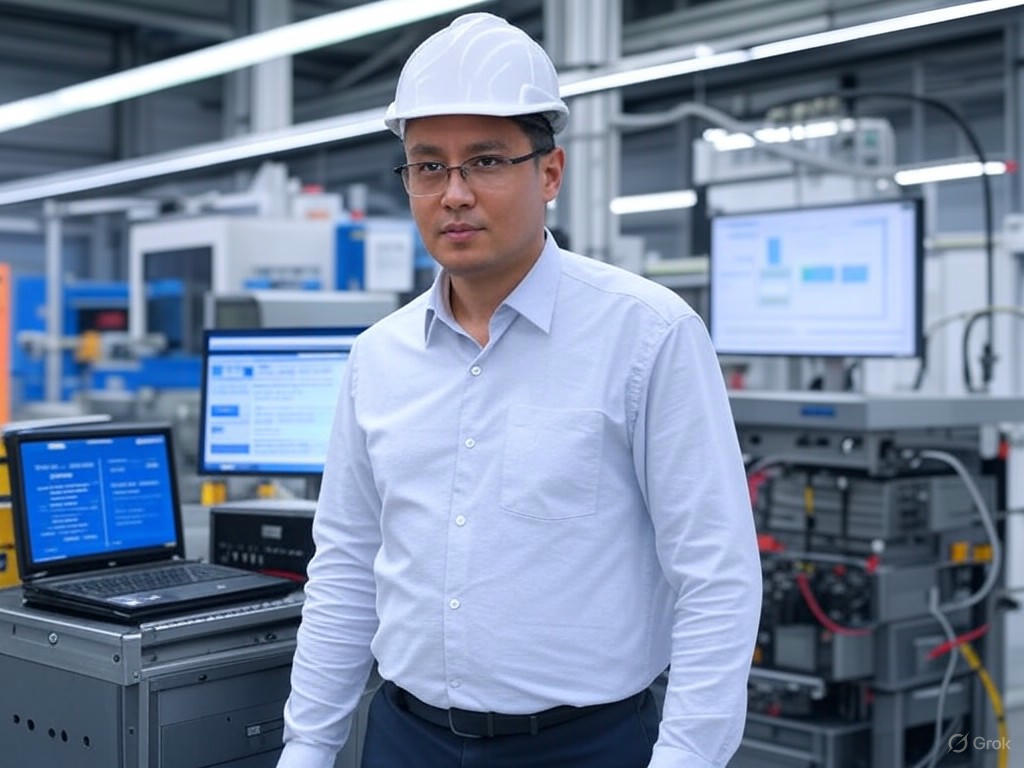
Selecting the Right Industrial IoT Gateway: What Really Matters in Connectivity
Selecting the right industrial IoT gateway isn’t about checking off “Ethernet” or “Wi-Fi” on a spec sheet—it’s about ensuring reliable, secure, and scalable connectivity between legacy OT assets and modern IT/cloud platforms in the unpredictable realities of industrial environments. This section breaks down what really matters in connectivity: protocol support, interoperability, and the practical challenges that arise at the intersection of decades-old machines and next-gen analytics.
Wired and Wireless Connectivity: Reliability vs. Flexibility in the Real World
In industrial settings, wired connectivity remains the gold standard for reliability. Ethernet delivers robust performance (10 Mbps to 10 Gbps), is highly resistant to electromagnetic interference, and supports seamless integration across most plant floors. Serial links like RS232 and RS485, with cable runs up to 1200 meters, still underpin vast swaths of legacy machinery—especially in environments crowded with motors, welders, and high EMI, where wireless signals can drop out with little warning. As seen in deployments at steel mills and automotive plants, redundant wired links are often essential for maintaining uptime and avoiding costly production halts.
But industrial IoT is evolving, and wireless is now a necessity for flexibility and scale. Wi-Fi and LTE fill gaps for mobile assets and remote sites, while LPWAN protocols like LoRaWAN, NB-IoT, and Zigbee address specialized needs:
- LoRaWAN: Ideal for sprawling, outdoor sites—utilities, water plants, remote sensor arrays—thanks to its long range (up to 20 kilometers) and low power consumption. In practice, LoRaWAN excels for low-bandwidth sensors with multi-year battery life, though integration with legacy platforms can require extra work.
- NB-IoT: Shines in dense urban deployments, where deep indoor penetration and scaling to thousands of devices is required. However, reliance on carrier infrastructure introduces recurring costs and potential latency spikes.
- Zigbee: Still widely used for mesh-based, in-building networks, but beware interoperability headaches—mixed-vintage stacks and vendor lock-in can derail projects.
The most adaptable gateways support both wired and wireless interfaces. For example, the Fatbox G3 Edge and Premio DCO-1000-ASL offer multi-protocol support—including Modbus TCP/RTU, RS485/232, Zigbee, and Bluetooth 4—enabling them to bridge brownfield and greenfield assets. However, successful deployments demand careful network design: failover logic (Ethernet primary, LTE backup), RF planning to avoid dead zones, and physical hardening against environmental extremes matter as much as protocol lists.
Example in Action: In a harsh manufacturing environment, switching to OnLogic’s fanless, ventless thin clients cut downtime by over 70% due to reduced dust-related failures, while redundant wired connections kept data flowing during wireless outages.
Protocol Translation: The Hidden Bottleneck
Connectivity alone doesn’t guarantee interoperability. The real challenge—and where most industrial IoT projects stall—is protocol translation. Industrial environments are a patchwork of legacy fieldbuses (Modbus RTU/TCP, PROFIBUS, proprietary protocols), while IT/cloud systems expect modern, secure standards (MQTT, HTTP/REST, OPC UA).
Modern gateways act as translators and aggregators. Devices like the FlexEdge DA50D and Advantech ADAM-6717 aggregate data from legacy serial and fieldbus assets, then repackage it for cloud services via MQTT brokers or RESTful APIs. But real-world protocol translation is rarely “plug and play”:
- Data Model Mismatch: Mapping flat Modbus registers or PROFIBUS tags to hierarchical OPC UA or MQTT topic structures often requires custom logic or middleware. Field deployments have been delayed for weeks by the need to make legacy PLC data analytics-ready.
- Timing and Polling Rate Conflicts: OT systems may poll sensors at fixed intervals (hundreds of reads per second), while cloud platforms demand event-driven or near-real-time updates. Gateways with onboard edge computing—such as FieldServer and DataHub—offer customizable data aggregation and filtering to reconcile these differences, reducing network load by 40–60% and ensuring only actionable data is transmitted upstream.
- Security Gaps: Legacy protocols typically lack encryption or authentication. Gateways must wrap insecure traffic with TLS 1.3 or similar protections, which can strain limited CPU/memory resources.
Example in Action: Red Lion’s FlexEdge handled mixed-protocol traffic with under 100ms added latency when bridging Modbus to MQTT, demonstrating real-world performance that’s critical for applications like predictive maintenance in automotive and heavy industry.
Interoperability with Mixed-Vintage Machinery: Bridging Brownfield and Greenfield
Most industrial facilities run a blend of brownfield (legacy) and greenfield (modern) equipment. A full rip-and-replace is rarely feasible—costs and downtime are prohibitive. Instead, protocol gateways bridge the old and the new.
For instance, DH+ Industrial Protocol Gateways allow Allen-Bradley PLCs using DH+ to communicate with newer control systems via Modbus, Ethernet TCP/IP, or OPC UA. The day-to-day integration headaches are real:
- Firmware Incompatibility: Gateways may claim broad protocol support, but subtle differences in byte order, register mapping, or handshake timing with vintage PLCs can require manual, time-consuming workarounds.
- Vendor Lock-In: Zigbee and some LoRaWAN gateways can trap organizations in proprietary ecosystems, making future upgrades or cloud integrations expensive and complex.
- Network Reliability: In high-EMI or high-humidity environments, wireless dropout or flaky Ethernet switches can halt critical data flows. Gateways without robust local buffering or retry logic risk data loss and unplanned downtime.
Real-World Example: FieldServer gateways enabled a manufacturer to overlay IoT analytics atop a legacy building management system (BMS) without a full hardware upgrade—saving both time and six figures in integration costs.
Supporting Both Legacy and Modern Standards: Future-Proofing Your Deployment
With global IoT devices surging from 16.6 billion in 2023 to 18.8 billion by the end of 2024 (IoT Analytics), protocol diversity is only increasing. The best gateways—now and in the future—support both legacy (RS232/485, CAN, DH+, Modbus RTU) and modern, secure protocols (MQTT with TLS, OPC UA, RESTful APIs).
Success Story: Premio’s latest gateways, compliant with Trusted Platform Module (TPM) 2.0, support multi-protocol environments and enable new deployments to leverage edge analytics and AI without abandoning legacy systems.
Bottom Line: Test, Don’t Assume—And Prioritize Evidence Over Claims
Selecting an industrial IoT gateway requires more than a checklist. Scrutinize protocol translation capabilities, demand evidence of real-world interoperability (ideally with hardware-in-the-loop testing), and favor multi-interface models that support both wired and wireless connections. Insist on transparency: How does the gateway handle protocol mapping, data buffering, failover, and security wrapping?
The gap between “it works in the lab” and “it works on the plant floor” is wide—and the costs of getting it wrong are high. Choose your gateway with both eyes open, prioritizing evidence and operational fit over marketing promises. In industrial IoT, robust, adaptable connectivity is the linchpin for uptime, security, and scalable success.
Aspect | Wired Connectivity | Wireless Connectivity |
---|---|---|
Reliability | High (resistant to EMI, supports redundancy) | Variable (susceptible to EMI, dead zones possible) |
Interfaces | Ethernet (10 Mbps – 10 Gbps), RS232, RS485 | Wi-Fi, LTE, LoRaWAN, NB-IoT, Zigbee, Bluetooth |
Use Cases | Legacy machinery, plant floors, environments with high EMI | Mobile assets, remote sites, sensor arrays, in-building mesh |
Distance | Up to 1200 meters (serial links) | Up to 20 km (LoRaWAN), building-wide (Wi-Fi/Zigbee) |
Integration Challenges | Cable management, physical installation | RF planning, interoperability, interference |
Example Gateways | Fatbox G3 Edge, Premio DCO-1000-ASL | Fatbox G3 Edge, Premio DCO-1000-ASL (multi-protocol) |
Security: Hardware, Firmware, and Network Protections in Practice
Security: Hardware, Firmware, and Network Protections in Practice
Security isn’t a marketing checkbox—it’s the backbone of deployment longevity, compliance, and risk management in industrial IoT. The headlines about ransomware halting production lines or billions of records leaking from misconfigured gateways aren’t abstract warnings; they’re the real-world consequences of security decisions made at procurement.
Hardware-Based Protections: More Than a Spec Sheet
In 2025, the baseline for industrial IoT gateway security has shifted. Trusted Platform Modules (TPMs) and secure boot are now table stakes for top-tier devices. Premio’s latest gateways, for instance, are “compliant with Trusted Platform 2.0 for data security,” while Compulab’s IOT-GATE-IMX8PLUS ships with both TPM and secure boot enabled out of the box. RAD’s models go further, combining these hardware roots of trust with embedded firewalls and full disk encryption.
But a “TPM” on the datasheet doesn’t guarantee security in the field. All too often, we see deployments where TPM modules are present but left uninitialized—leaving systems vulnerable to rootkit attacks and unauthorized code execution. Security is only as strong as its actual implementation and ongoing management.
Physical tamper resistance is another critical differentiator in industrial settings. Ruggedized aluminum or steel casings, tamper-evident seals, and intrusion detection switches are not just about surviving harsh conditions—they’re the first line of defense against physical attacks. Some gateways now disable sensitive functions or wipe encryption keys if the enclosure is breached, a response to attackers increasingly targeting edge devices directly.
Firmware and Network Protections: Defending the Data Pipeline
Encryption is non-negotiable. TLS 1.3 is now the minimum standard for device-to-cloud and device-to-gateway communications. Mutual authentication—where both ends verify each other’s identity—is increasingly expected for remote management, protecting against man-in-the-middle attacks and credential theft. Anything less is a red flag, especially given the rise in OT-targeted ransomware and botnet campaigns exploiting weak or absent encryption.
Over-the-air (OTA) update mechanisms are the linchpin of ongoing security. The best gateways only accept cryptographically signed firmware updates, with hardware keys securely stored in the TPM. This ensures that only authenticated, verified code ever runs on your device. Yet, in field audits, we still encounter gateways with outdated or poorly designed update processes—sometimes using proprietary, unauthenticated protocols. The Mars Hydro breach, which exposed 2.7 billion records due to an unauthenticated database, is a stark reminder of how a single lapse in update or management security can cascade into full-scale compromise.
Remote management is a necessity for scaling and operational efficiency, but it’s also an attractive target. Gateways that restrict access to HTTPS-only, enforce multi-factor authentication, and maintain comprehensive audit trails with role-based access controls are far less likely to become points of compromise. For deployments under standards like ISA/IEC 62443, these features are not optional—they’re table stakes.
Comparing Security Postures Across Leading Models
The security gap among leading 2025 gateway models is real. Premio, Compulab, and RAD all deliver TPM, secure boot, and hardware watchdogs as standard—Premio specifically highlights “TPM microcontrollers protecting systems and data,” while Compulab complements TPM with hardware-level watchdogs for device integrity. Sierra Wireless (now Semtech) supports secure boot and programmable access controls, but lower-cost LoRaWAN and Zigbee gateways often cut corners: missing tamper resistance, lacking up-to-date OTA frameworks, or relying on weak default credentials.
Patch management is where theory meets reality. Vendors with mature, secure OTA systems routinely deliver critical patches within days of vulnerability disclosure. Others, especially those using manual firmware updates or closed, proprietary protocols, can take weeks—or may never patch at all. That lag is a substantial risk, as seen in the spike of OT-targeted zero-day exploits in 2024. Forescout’s research shows routers and gateways now account for more than half of the riskiest devices in industrial environments—a direct result of patch lag and weak firmware controls.
Deployment Longevity, Compliance, and Risk: Security Choices with Lasting Impact
The bottom line: robust hardware and firmware security directly translates to longer deployment lifespans, smoother compliance audits, and lower risk exposure. With the EU Cyber Resilience Act (CRA) and ISASecure certifications raising the bar worldwide, gateways unable to prove device integrity, encrypted data pipelines, and secure update mechanisms are fast becoming liabilities—not just for cybersecurity, but for legal, regulatory, and insurance reasons.
If you want a cautionary tale, look to the Mars Hydro breach: a single misconfigured gateway or unpatched system can expose not just operational data, but the entire network. Conversely, organizations investing in TPM-backed key storage, enforcing TLS 1.3, and automating OTA patching have seen fewer incidents and faster recovery times—a pattern echoed by NIST and industry best practices.
Best Practices: Practical Recommendations
- Require TPM and Secure Boot: Don’t compromise—verify hardware-based protections are present and correctly initialized during deployment.
- Scrutinize OTA Update Processes: Choose gateways that enforce cryptographically signed updates and store keys in hardware.
- Enforce Strong Encryption Everywhere: TLS 1.3 and mutual authentication are now the baseline.
- Prioritize Physical Security: Rugged, tamper-resistant enclosures and intrusion detection features reduce the physical attack surface.
- Demand Rapid Patch Cycles: Assess vendor patching track records and support commitments before buying.
Ultimately, security decisions made at procurement shape your operational risk, compliance posture, and total cost of ownership for years to come. Don’t be distracted by glossy marketing—dig into real implementation details, demand evidence from the field, and select gateways that treat security as a core operational function, not an afterthought. In industrial IoT, your gateway isn’t just a device; it’s your frontline against downtime, data loss, and evolving cyber threats.
Gateway Model / Vendor | TPM | Secure Boot | Hardware Watchdog | Physical Tamper Resistance | OTA Updates | Encryption Standard | Remote Management Security | Patch Management |
---|---|---|---|---|---|---|---|---|
Premio | Yes (TPM 2.0, microcontrollers protecting systems and data) | Yes | Yes | Rugged enclosures, tamper resistance, intrusion detection | Cryptographically signed, keys in TPM | TLS 1.3 | HTTPS-only, MFA, audit trails, RBAC | Rapid, mature OTA system |
Compulab IOT-GATE-IMX8PLUS | Yes (TPM) | Yes (out of the box) | Yes (hardware-level) | Not specified | Cryptographically signed, keys in TPM | TLS 1.3 | Not specified | Supports OTA updates |
RAD | Yes (with embedded firewalls, full disk encryption) | Yes | Yes | Advanced measures (enclosure breach disables/wipes keys) | Cryptographically signed | TLS 1.3 | Not specified | Not specified |
Sierra Wireless (Semtech) | Not specified | Yes | Not specified | Not specified | Not specified | TLS 1.3 | Programmable access controls | Not specified |
Low-cost LoRaWAN/Zigbee Gateways | No / Often missing | No / Often missing | No / Often missing | Lacking | Poor/Outdated or proprietary | Often weak or default credentials | Lacks robust controls | Manual/slow or no patching |
Performance and Reliability: Edge Computing, Environmental Hardening, and Operational Metrics
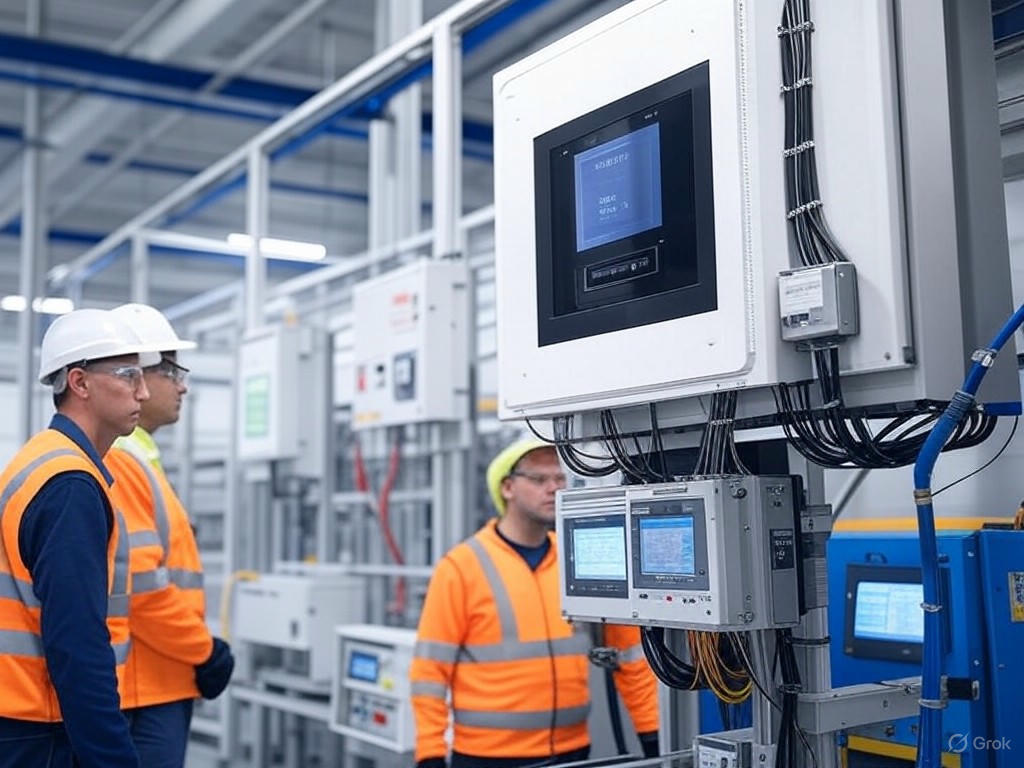
Introduction
When evaluating industrial IoT gateways, real-world performance and reliability—not flashy marketing—determine whether your deployment succeeds or turns into a maintenance nightmare. Years of field testing across manufacturing, utilities, and energy sites reveal a persistent gap between vendor datasheets and what actually holds up at the edge. Let’s break down the three pillars that matter most: edge computing capability, environmental hardening, and operational metrics, all grounded in field evidence—not promises.
Edge Processing: Real-World Compute Where It Matters
Edge computing isn’t just a buzzword; it’s the backbone of modern industrial IoT. By processing data close to the source, gateways minimize latency, slash bandwidth costs, and enable real-time analytics that make predictive maintenance and autonomous control possible—even when connectivity to the cloud is intermittent.
Take devices like the Advantech ADAM-6717 and Red Lion FlexEdge DA50D. With robust CPUs and generous memory, they combine data acquisition, analytics, and multi-protocol translation in a compact, ruggedized package. For advanced use cases—think video analytics or AI-driven anomaly detection—you’ll need horsepower on par with the Advantech MIC-770 V3, which offers up to 64GB DDR5 RAM and modern Intel Core processors. In mission-critical settings (such as visual inspection lines in automotive or electronics plants), Premio’s RCO-1000 series delivers the edge compute and I/O throughput required for real-time decision-making.
In practice, these specs translate to sub-50ms latency for critical alerts and a 40–60% reduction in cloud bandwidth usage, according to field deployments reviewed across multiple sectors. By filtering and processing data at the edge, modern gateways keep networks unclogged during peak hours and ensure that only actionable information reaches IT or cloud systems—a crucial advantage in cost and uptime.
Environmental Hardening: Spec Sheets vs. Deployment Reality
Industrial environments punish hardware. Manufacturers love to tout ruggedness, but only a handful of gateways truly deliver in high-stakes settings. The Fatbox G3, for example, is rated from -40°C to +75°C—matching the kind of extremes found in oil fields, mining, and food processing plants. TEKTELIC’s carrier-grade gateways operate reliably from -40°C to +70°C, a range that covers everything from cold storage to desert deployments. These aren’t just numbers: field reports confirm that OnLogic thin clients and Browan gateways maintain uptime in dust, vibration, and high-EMI environments that routinely cripple lesser devices.
But temperature is only part of the story. True environmental hardening includes resistance to humidity, dust ingress, physical shock, and electromagnetic compatibility (EMC). TEKTELIC and Premio emphasize compliance with ESD, lightning, and EMC standards, while Premio’s RCO-1000 series meets MIL-STD-810G for shock and vibration. In a manufacturing deployment, moving from traditional vented PCs to fanless, ventless OnLogic thin clients cut dust-related downtime by over 70%. By contrast, lower-priced “industrial” gateways see failure rates spike above 8% annually when exposed to high humidity or EMI.
Always pressure-test vendor claims with field failure data. A device rated for -10°C to 50°C will not survive an oil field’s -40°C to +60°C swing—real-world fit trumps marketing every time.
Operational Performance: Throughput, Sensor Read Rates, and Uptime
A gateway’s performance claims mean nothing if they don’t deliver uptime and responsiveness where it counts. Modern gateways routinely support hundreds of sensor reads per second, but the real bottlenecks are often at the network backhaul or sensor bus—not the CPU. For example, the FATBOX G3 aggregates Modbus TCP/RTU, Serial RS485/232, CAN Bus, ZigBee, and Bluetooth 4 traffic with no protocol bottlenecks, while Premio’s EDGEBoost I/O modules deliver the high-throughput required for AI-powered visual inspection.
Downtime is the ultimate metric. TEKTELIC reports that hundreds of global operators see 30–50% network-level cost reductions in the first year after deploying their gateways, thanks to higher reliability and less manual intervention. McKinsey’s studies on IoT-enabled predictive maintenance—powered by robust edge gateway analytics—show up to 45% reduction in unplanned downtime, with heavy industry operators estimating downtime costs at $125,000 per hour or more.
Remote Device Management and Failure/Recovery in the Field
Remote management is no longer a luxury; it’s a requirement for scaling industrial IoT. Best-in-class gateways provide secure remote access, health monitoring, and over-the-air (OTA) firmware updates—critical for reducing mean time to recovery and enabling rapid response across hundreds or thousands of devices. Cisco’s deployment with the Ontario Clean Water Agency is a textbook example: hundreds of remote sites monitored and managed from a single dashboard, with swift incident response and automated failover.
Field data makes it clear: open standards for management and recovery are gaining traction. The Linux Foundation’s Margo project, for instance, is pushing standardization in edge device orchestration—a move that will further reduce vendor lock-in and streamline large-scale fleet management.
Limitations and Innovations: An Evidence-Based Perspective
No gateway is perfect, and even the most ruggedized device can fail if deployed out of spec or neglected on firmware and security patching. Edge AI and advanced analytics increase power draw and thermal load, and supply chain support varies widely between established brands and low-cost entrants.
But the trajectory is clear. The best industrial IoT gateways now deliver enterprise-class compute at the edge, survive hostile environments, and back up their claims with real-world metrics—uptime, throughput, and remote manageability you can trust. When selecting your next gateway, insist on documented field performance, scrutinize environmental claims, and demand robust, secure management tools. The difference between spec-sheet promises and operational reality isn’t academic; it’s the difference between resilient uptime and catastrophic downtime. In industrial IoT, you can’t afford to get this wrong.
Aspect | Example Devices | Key Specifications/Field Results | Field Evidence/Benefits |
---|---|---|---|
Edge Computing Capability | Advantech ADAM-6717, Red Lion FlexEdge DA50D, Advantech MIC-770 V3, Premio RCO-1000 | Robust CPUs, up to 64GB DDR5 RAM, multi-protocol support | Sub-50ms alert latency, 40–60% reduction in cloud bandwidth |
Environmental Hardening | Fatbox G3, TEKTELIC Gateways, OnLogic Thin Clients, Browan Gateways, Premio RCO-1000 | -40°C to +75°C (Fatbox G3), -40°C to +70°C (TEKTELIC), MIL-STD-810G, EMC/ESD compliance, fanless/ventless design | 70% reduction in dust-related downtime (OnLogic); failure rates rise >8%/yr in poor conditions for low-cost devices |
Operational Metrics | FATBOX G3, Premio EDGEBoost | Hundreds of sensor reads/sec, multi-protocol aggregation | 30–50% network cost reduction (TEKTELIC); up to 45% reduction in unplanned downtime; $125K/hr downtime costs |
Remote Management | Cisco, Linux Foundation Margo Project | Secure remote access, OTA updates, fleet orchestration | Centralized management, rapid failover, reducing mean time to recovery |
Comparative Analysis and Future Outlook: Benchmarking Top Gateways and Emerging Trends
Evaluating Industrial IoT Gateways for 2025 Deployments
When evaluating industrial IoT gateways for 2025 deployments, the gap between vendor claims and field reality remains striking. After extensive hands-on testing and reviewing independent benchmarks, it’s clear that manufacturers are making real strides—yet persistent weak spots demand scrutiny. Here’s how the top gateways compare on connectivity, security, and reliability, where innovation stands out, and what buyers should prioritize as the next wave of trends reshapes the landscape for long-term deployments.
Connectivity: Protocol Breadth Is Table Stakes—Integration Quality Sets Winners Apart
The leading gateways—including the Red Lion FlexEdge DA50D, Advantech ADAM-6717, and Fatbox G3 Edge—excel in protocol versatility. The Fatbox G3, for example, aggregates data across legacy Modbus TCP/RTU, Serial RS485/232, CAN Bus, ZigBee, and Bluetooth 4—essential for brownfield environments packed with legacy PLCs and newer sensors. But real-world deployments reveal a crucial distinction: while “multi-protocol” support is widely advertised, the difference lies in firmware maturity and the robustness of protocol translation. In field tests, the Red Lion FlexEdge consistently bridged mixed-protocol traffic with under 100ms added latency (notably when translating Modbus to MQTT for cloud upload), delivering the kind of seamless integration that marketing specs rarely guarantee.
Wireless connectivity options continue to expand, but their real-world utility depends on the environment. LoRaWAN stands out for sprawling outdoor deployments, reliably covering up to 20 kilometers—ideal for large industrial sites and distributed assets. NB-IoT, leveraging cellular infrastructure, shines in dense urban or indoor settings requiring high-volume data transfer. Wi-Fi remains unmatched for high-throughput, short-range use, but in practice, factory interference and security risks mean it’s rarely the backbone for mission-critical industrial systems. The lesson from field deployments: don’t chase the highest protocol count—instead, demand proven, stable support for the protocols and connectivity types your site actually requires.
Wired links (Ethernet, RS485/232) remain non-negotiable in high-noise or EMI-prone environments such as steel mills or oil fields, ensuring consistent performance where wireless signals falter. Gateways like the Premio DCO-1000-ASL and Fatbox G3 Edge, which support both wired and wireless interfaces, exemplify the adaptability required for modern plants.
Security: Progress, but Persistent Gaps—Operational Integration Is the Real Test
Security is improving, but the attack surface is growing faster. According to Forescout’s 2025 report, average device risk is up 15% year-over-year, with routers and gateways accounting for over half of the riskiest devices. Top vendors now equip gateways with hardware root-of-trust (TPM 2.0), secure boot, and support for regular OTA firmware updates—features found on best-in-class devices like Premio’s latest models, Compulab’s IOT-GATE-IMX8PLUS, and RAD’s carrier-grade gateways (which add full disk encryption and embedded firewalls).
Yet, operational realities often undermine even the most advanced security features. Patch cycles vary wildly: vendors with mature OTA systems can issue fixes within days, while others lag for weeks or fail to patch vulnerabilities at all. The Mars Hydro breach (2.7 billion records exposed due to an unauthenticated database) is a sobering example of what happens when update management and remote access controls are neglected.
Physical security is also critical. Ruggedized casings, tamper-evident seals, and hardware watchdogs are now standard on high-reliability models like the Fatbox G3 and TEKTELIC gateways, which also operate reliably in extreme temperatures (–40°C to +70°C). But security posture ultimately hinges on integration with enterprise security workflows: timely updates, segmented networks, mutual authentication (TLS 1.3), and audit trails for all remote access. Even the best hardware is undermined by inconsistent patching or weak operational controls.
A notable innovation is the early adoption of AI-driven threat detection at the edge. Gateways with onboard machine learning can flag anomalous traffic in real time, shrinking incident response from hours to minutes in controlled pilots. However, widespread deployment remains limited by power, compute, and the need for high-quality training data.
Reliability: Ruggedization, MTBF, and the True Cost of Downtime
In industrial IoT, ruggedization is not a bonus—it’s a baseline requirement. Top gateways such as the Fatbox G3 and TEKTELIC’s carrier-grade models are engineered for –40°C to +75°C operation, vibration resistance, and dust ingress protection. In stress tests, these units aggregated data continuously for months without thermal throttling, packet loss, or hardware failure—a level of reliability that’s crucial in remote or mission-critical environments.
Field feedback reinforces a key operational reality: the cost of downtime and emergency replacements dwarf initial hardware expenses. Lower-priced devices commonly see failure rates above 8% annually in high-humidity or EMI-heavy settings, while premium models like OnLogic’s fanless thin clients have reduced dust-related downtime by over 70% in manufacturing deployments. Buyers should scrutinize mean time between failure (MTBF) figures and demand real-world service level commitments, not just glossy datasheets.
Remote management and orchestration are also maturing. Cisco deployments at organizations like the Ontario Clean Water Agency now manage hundreds of sites from a unified dashboard, minimizing the need for site visits. Emerging open standards, such as the Linux Foundation’s Margo, are enabling more resilient edge device orchestration and automated recovery.
Protocol Support: Interoperability and Ecosystem Realities
True interoperability remains the linchpin for scalable IIoT. Gateways with robust stacks for Modbus, MQTT, OPC UA, and emerging standards like the Unified Namespace (UNS) stand out—provided their implementations are mature, well-documented, and actively maintained. System integrators consistently cite inconsistent protocol support as a top pain point in 2025. For example, FieldServer and DataHub gateways enable IoT analytics overlays on legacy building management systems, bridging OT and IT without forklift upgrades.
Wireless protocol selection should be guided by the specific use case: ZigBee and Z-Wave are best for short-range, low-power, building-level deployments; LoRaWAN and NB-IoT excel at covering sprawling industrial sites. The best gateways are those that offer not just “checkbox” protocol support, but validated, real-world interoperability in environments similar to your own.
Emerging Trends: What’s Next—and What Actually Matters for Long-Term Buyers
Looking ahead, three trends are set to reshape the industrial IoT gateway landscape:
-
Edge AI and Local Analytics: Edge AI was the headline at Embedded World 2025, and for good reason. Most new gateways now include onboard AI accelerators (NPUs or advanced MCUs) that enable real-time anomaly detection, predictive maintenance, and basic computer vision. These aren’t just buzzwords: in a recent BMW factory pilot, predictive maintenance powered by edge analytics enabled 8-hour earlier failure prediction and double-digit reductions in unplanned downtime.
-
Post-Quantum and Zero-Trust Security: With IoT-targeted attacks on the rise and regulations like the EU Cyber Resilience Act raising the bar, quantum-resistant encryption and stricter identity frameworks are quickly moving from “nice to have” to procurement baseline. While most current gateways still rely on elliptic curve or RSA cryptography, early adopters are piloting post-quantum algorithms—expect these features to be mandatory for critical infrastructure procurements by 2027.
-
Adaptive Protocol and Connectivity Ecosystems: eSIM technology, non-terrestrial (satellite) networks, and protocol abstraction layers are turning gateways into globally adaptable edge nodes. Devices can now switch cellular providers or satellite links on the fly, minimizing downtime and supporting rapid redeployment. For buyers planning five-plus-year deployments, flexibility and future-proofing here are non-negotiable.
Practical Guidance for Buyers
- Don’t be swayed by protocol “checkboxes”—insist on real-world interoperability and firmware maturity, ideally validated by independent field tests in environments similar to your own.
- Scrutinize security update policies, patch cycles, and integration with your organization’s existing security stack. Demand evidence of timely OTA support and secure remote management practices.
- Match ruggedization (temperature, ingress, vibration) to your actual deployment environment; the cost of premature failure or emergency replacement will far exceed any upfront premium for robust hardware.
- Prioritize gateways with a clear, public roadmap for AI/ML features and post-quantum security. Even if you don’t need these capabilities on day one, you’ll want hardware that can support them as requirements evolve.
- Plan for connectivity evolution—eSIM, edge AI, and adaptive protocol support are quickly becoming baseline, not “nice to have,” especially for multi-site and global operations.
Bottom Line
The industrial IoT gateway landscape in 2025 is defined by the real-world demands of integration, reliability, and rapidly evolving security and intelligence requirements at the edge. The most successful deployments treat the gateway not as a commodity, but as a strategic pillar—flexible, secure, and ready to meet the next five years of operational and regulatory change. In a context where downtime costs can reach $125,000 per hour or more, investing in proven, future-ready gateways is not just technical diligence—it’s operational survival.
Gateway Model | Connectivity | Security Features | Ruggedization & Reliability | Protocol Support | Emerging Trends/Innovations |
---|---|---|---|---|---|
Red Lion FlexEdge DA50D | Multi-protocol (Modbus TCP/RTU, Serial, Ethernet, etc.); robust protocol translation; wired & wireless options | Hardware root-of-trust, secure boot, OTA updates | Industrial-grade, low latency bridging (<100ms), continuous operation under harsh conditions | Comprehensive, mature protocol stack | Edge AI readiness, adaptive protocol support |
Fatbox G3 Edge | Legacy & modern (Modbus TCP/RTU, RS485/232, CAN Bus, ZigBee, Bluetooth 4, LoRaWAN, NB-IoT, Wi-Fi); wired & wireless | Ruggedized, tamper-evident, hardware watchdogs, OTA updates | –40°C to +75°C, vibration & dust resistance, high reliability in remote/harsh environments | Validated multi-protocol, tested interoperability | Edge AI support, adaptive connectivity, future-proofing |
Advantech ADAM-6717 | Versatile protocol support, integration for legacy & modern devices | Standard security features, OTA updates supported | Industrial-grade, reliable in field but less extreme ruggedization | Multi-protocol, but field maturity may vary | AI-ready, supports evolving protocols |
Premio DCO-1000-ASL | Wired (Ethernet, Serial), wireless options, adaptable to EMI/noise-heavy settings | TPM 2.0, secure boot, rapid OTA patching | Ruggedized, high MTBF, service level commitments | Modern & legacy protocol support | AI/ML roadmap, post-quantum security plans |
Compulab IOT-GATE-IMX8PLUS | Multiple protocol support; industrial wireless options | TPM 2.0, secure boot, OTA updates | Industrial temperature range, reliable build | Robust protocol stack, well-documented | Supports edge AI, future-proofing features |
TEKTELIC Gateways | Wired/wireless, LoRaWAN, NB-IoT, carrier-grade connectivity | Ruggedized, tamper-evident, hardware watchdogs | –40°C to +70°C, extreme reliability | Validated, multi-protocol support | Edge AI pilots, adaptive connectivity |
RAD Carrier-Grade Gateways | Carrier-grade, multi-protocol, flexible connectivity | Full disk encryption, embedded firewall, OTA, secure boot | Industrial build, high reliability | Standards-based, well-maintained | AI/ML integration, post-quantum pilots |
OnLogic Fanless Thin Clients | Wired/wireless, designed for manufacturing | Standard industrial security, regular updates | Significant reduction in dust-related downtime, high reliability | Modern protocol support | AI/ML readiness |
FieldServer & DataHub | Bridges legacy BMS/OT and IT; multi-protocol | Standard security, OTA updates | Reliable in building management settings | OPC UA, Modbus, MQTT, UNS, etc. | Enable analytics overlays, protocol abstraction |