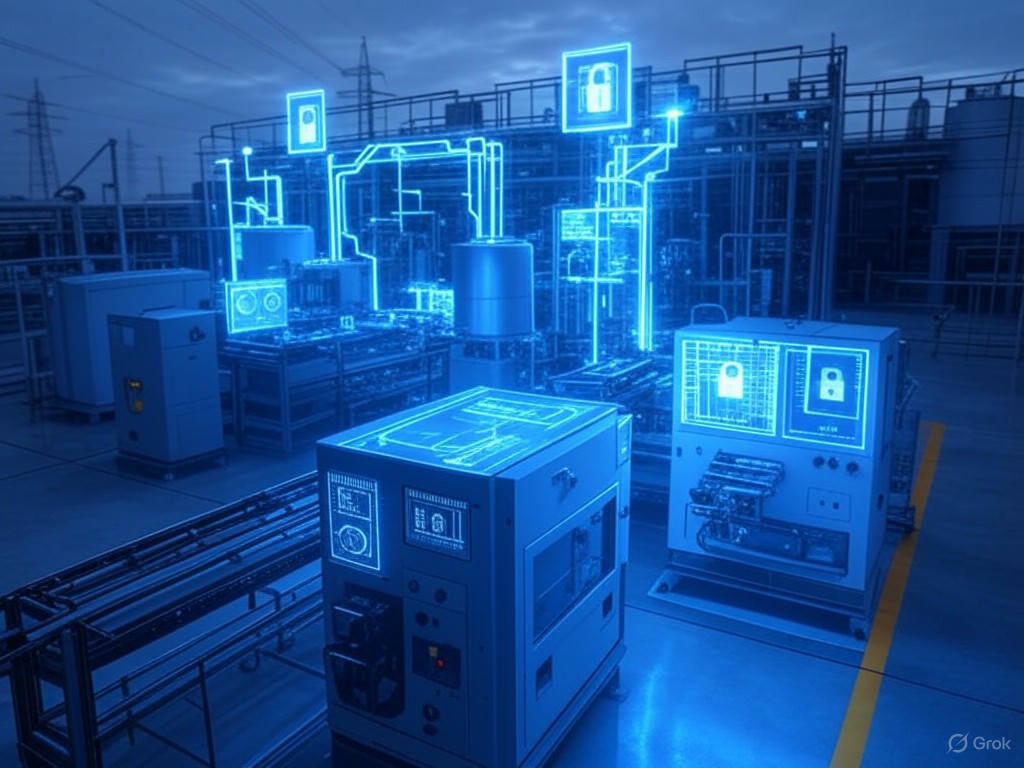
Securing Industrial IoT: Proven Strategies for Manufacturing & Utilities
- Introduction: Why Securing Industrial IoT Devices Can No Longer Be an Afterthought
- The Case for Securing Industrial IoT (IIoT) Devices
- What Is IIoT, and Why Does It Matter?
- Expanding Attack Surface: Real-World Risks and Consequences
- IIoT Security Goals: Why Proactive Beats Reactive
- Attack Trends and Regulatory Drivers: The Evidence
- The Bottom Line
- Prerequisites and Baseline: What You Need to Know Before Securing IIoT
- Introduction
- 1. Asset Inventory: The Non-Negotiable Starting Point
- 2. Understand Industrial Protocols and Legacy Constraints
- 3. Know the Risks of Legacy and Heterogeneous Systems
- 4. Baseline Security Policies and Vendor Management
- 5. Checklist: Is Your Organization Ready?
- Common Gaps in Real Deployments
- Bottom Line
- Core Steps to Secure Industrial IoT Devices: Practical, Evidence-Based Methods
- 1. Asset Inventory and Risk Assessment: Visibility is Non-Negotiable
- 2. Network Segmentation: Contain Threats, Prevent Lateral Movement
- 3. Secure Device Onboarding and Lifecycle Management: Lock Down the Supply Chain
- 4. Authentication, Credential Management, and Access Controls: Eliminate the Low-Hanging Fruit
- 5. Encrypted Communications: Don’t Let Data Travel in the Clear
- 6. Patching and Vulnerability Management: Relentless, Not Occasional
- 7. Real-Time Monitoring and Anomaly Detection: Move from Luck to Certainty
- Conclusion: Relentlessly Execute the Proven Fundamentals
- Benchmarking and Comparative Analysis: What Works, What Fails, and Real-World Lessons
- Benchmarking and Comparative Analysis: What Works, What Fails, and Real-World Lessons
- No Silver Bullet: Context Rules the Security Game
- Comparing the Big Three: Zero Trust, Secure by Design, and Vendor-Integrated Platforms
- Performance Benchmarks: Detection, Response, and Real-World Metrics
- Measuring Security Maturity and ROI: Lessons from the Field
- User Experience: What Actually Works in the Field
- Bottom Line
- Troubleshooting, Advanced Optimizations, and Next Steps
- Navigating IIoT Security Challenges in Manufacturing and Utilities
- Troubleshooting Common IIoT Security Challenges
- Device Visibility Gaps
- Legacy System Integration
- False Alarms and Alert Fatigue
- Remote Access Vulnerabilities
- Advanced Optimizations for Experienced Teams
- AI-Driven Threat Detection
- Automated Incident Response
- Secure Cloud and Edge Integration
- Next Steps: Continuous Improvement and Staying Ahead
- Iterative Security Cycles
- Ongoing Staff Training
- Anticipate Evolving Threats
- Resources for Ongoing Learning and Adaptation
- Key Takeaways
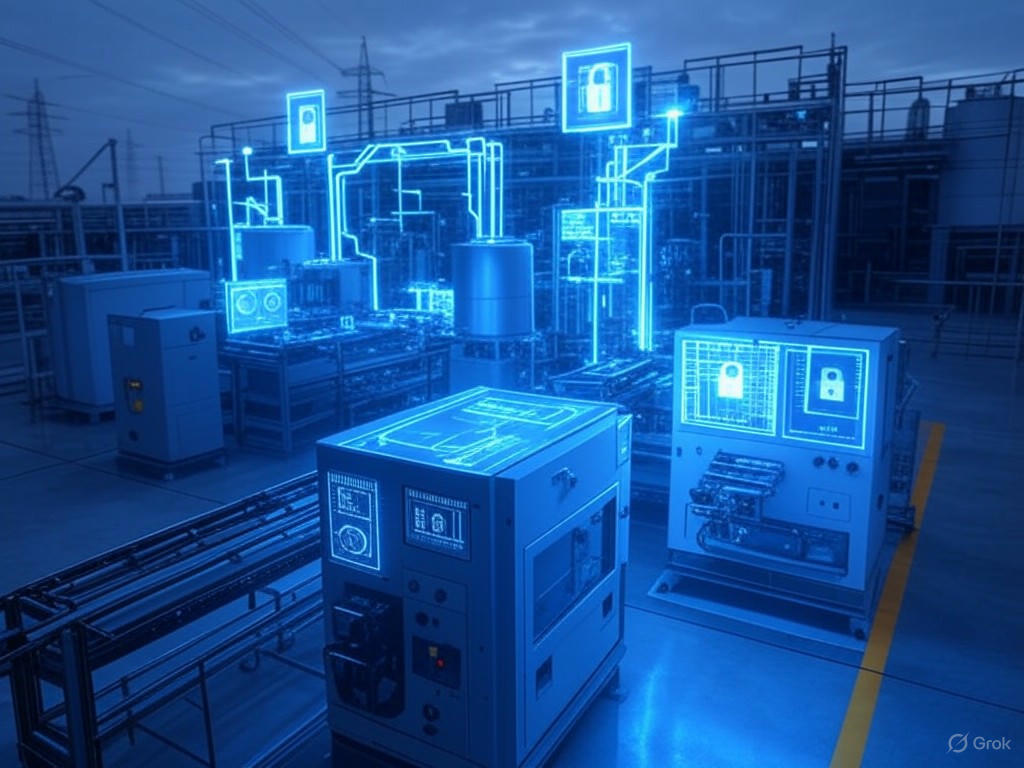
Introduction: Why Securing Industrial IoT Devices Can No Longer Be an Afterthought
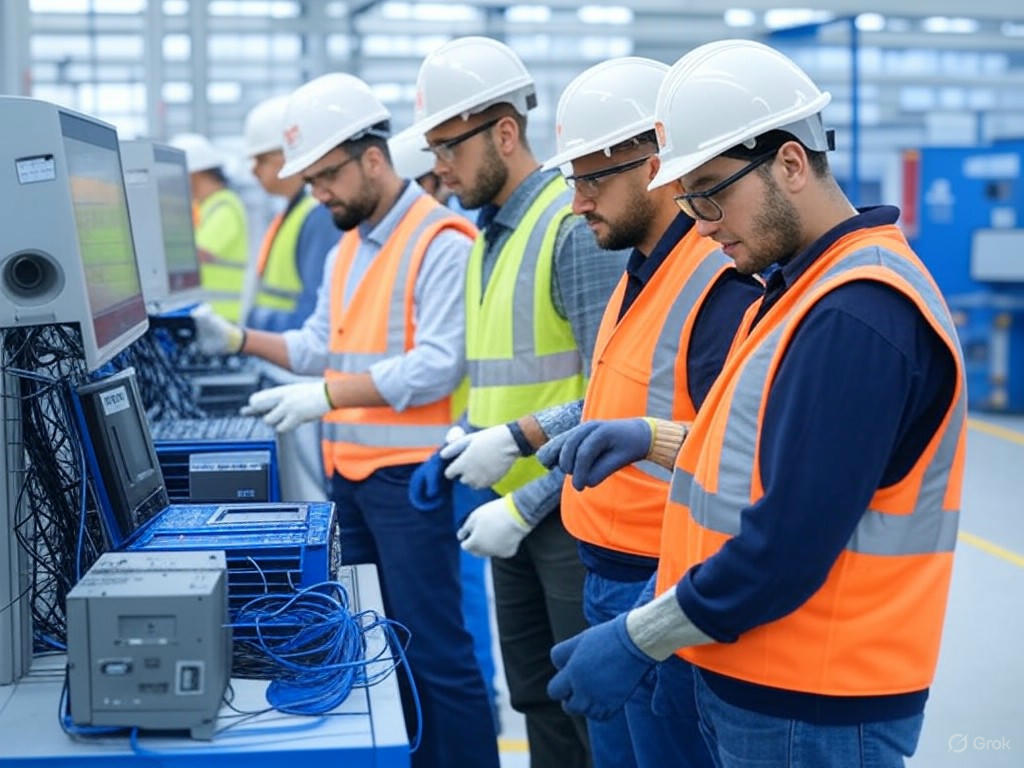
The Case for Securing Industrial IoT (IIoT) Devices
The case for securing industrial IoT (IIoT) devices is no longer hypothetical—it’s an operational necessity for manufacturing and utilities. The rapid rise in IIoT adoption has delivered undeniable efficiency gains, but it has also exposed critical infrastructure to a host of new—and rapidly evolving—attack vectors. The numbers are stark: manufacturing organizations have seen a 300% surge in cyberattacks since 2019 (Hoxhunt), and over 80% of companies now report at least one IoT-related security breach. Ransomware, data manipulation, and supply chain attacks have become routine disruptions, targeting sectors once considered immune to digital threats.
What Is IIoT, and Why Does It Matter?
Industrial IoT refers to the integration of networked sensors, edge devices, and intelligent controllers into environments such as factories, power grids, and water treatment plants. Unlike consumer IoT, IIoT is laser-focused on optimizing industrial processes, enabling predictive maintenance, and unlocking real-time visibility into assets that were previously “black boxes.” In practice, IIoT enables:
- Predictive Maintenance: 61% of organizations cite this as their top IIoT use case, with predictive analytics reducing unplanned downtime by up to 45% and saving millions per production line (GE Vernova, McKinsey).
- Remote Monitoring and Control: Manufacturers and utilities now oversee and respond to system anomalies from anywhere—an essential capability during the COVID-19 supply chain crisis (ATS, T&D World).
- Real-Time Data and Automation: AI-driven analytics and edge computing streamline production, boost asset reliability, and support grid modernization.
- Scalability and Adaptability: Smart factories and digital utilities deploy IIoT solutions to adapt to mass customization and fluctuating energy demands; by 2025, 70% of companies are actively developing or deploying IIoT strategies (HiveMQ).
IIoT is now the backbone of industrial competitiveness. But every new connection expands the attack surface.
Expanding Attack Surface: Real-World Risks and Consequences
Every connected device is a potential attack vector. The convergence of operational technology (OT) and IT has “dramatically expanded the attack surface,” leaving critical infrastructure exposed to increasingly sophisticated threats (Nomios Group, TXOne). Manufacturing has topped the ransomware target list for three consecutive years, with a 102% year-over-year spike in ransomware victims and 70 active ransomware groups in Q1 2025 alone (Smart Industry, GuidePoint Security).
The core risks include:
- Ransomware and Data Manipulation: Data manipulation is now the most common attack method in manufacturing, energy, and utilities (Nozomi Networks). Ransomware routinely halts production lines and disrupts energy grids, causing average downtime of 6.5 hours per incident.
- Supply Chain Vulnerabilities: 64% of significant incidents now originate from third-party vendor vulnerabilities (Kiteworks). The Change Healthcare breach exemplifies how supply chain attacks can cascade across entire industries.
- Device Vulnerabilities: Over 50% of IoT devices have critical, unpatched vulnerabilities, and one in three data breaches involves an IoT device (JumpCloud). Unpatched firmware accounts for 60% of all breaches.
- Downtime and Safety Risks: Cyberattacks on IIoT networks cost heavy industry an average of $125,000 per hour of downtime, with some incidents exceeding $1 million per hour. In extreme cases, attacks have triggered power grid failures and physical equipment sabotage (Aon, PT Cyber Analytics).
These are not theoretical risks. The Ukraine power grid attack, the exposure of widespread OT vulnerabilities by hacktivist groups, and high-profile incidents like the American Water Works breach (October 2024) prove that a single exploit can take entire regions offline or endanger public safety.
IIoT Security Goals: Why Proactive Beats Reactive
In IIoT, the stakes are higher than in traditional IT. Here, the principal security objectives are clear: maintain uptime, ensure data integrity, and protect the safety of people and assets. A breach doesn’t just mean lost data—it means halted production, environmental damage, and genuine threats to human life (Claroty).
Yet, nearly three in five organizations still rely on reactive security—responding only after threats materialize or damage occurs (Smart Industry/Armis). Meanwhile, 81% of IT leaders now recognize that a proactive approach is essential, but actual implementation lags far behind.
The imperatives for IIoT security are:
- Continuous Monitoring: Real-time anomaly detection is essential for spotting threats before they cause downtime, leveraging AI-driven platforms for sub-15-minute detection (UptimeRobot, Scientific Reports 2024).
- Network Segmentation and Zero Trust: The traditional “air gap” is obsolete. Zero trust—verifying every user, device, and connection—is the baseline even for legacy OT environments (Industrial Cyber, Vigilant Asia).
- Device Authentication and Encryption: Secure onboarding, mutual authentication, and encrypted communications (TLS 1.3) are now table stakes, not optional extras (NIST, T&D World).
- Regulatory Compliance: Industrial cybersecurity is increasingly shaped by regulatory mandates. In the EU, NIS2 and EN 18031-1:2024 set strict requirements for critical infrastructure; in the US, NIST guidance drives industry best practices. Non-compliance risks steep fines and reputational harm, particularly in regulated sectors (IoT Insider, NIST).
Attack Trends and Regulatory Drivers: The Evidence
Attackers are becoming more sophisticated, leveraging AI to supercharge attacks and exploit the complexity of modern industrial environments (Smart Industry/Armis, SentinelOne). Advanced Persistent Threat (APT) groups, ransomware operators, and hacktivists now routinely target manufacturing, energy, and utilities, with risks intensifying amid geopolitical tensions (IIoT World, PT Cyber Analytics).
Regulation is rapidly catching up. The EU’s NIS2 directive and the US’s ongoing NIST framework updates are raising the bar, mandating risk assessments, incident reporting, and secure-by-design requirements. Certification standards such as ISA/IEC 62443 and ISASecure are increasingly demanded by customers and regulators alike. The market is responding, with major investments in integrated cybersecurity platforms from vendors like Siemens, Microsoft, AWS, and PTC (Gartner Peer Insights, SiliconANGLE).
The Bottom Line
Industrial IoT has become indispensable for operational excellence in manufacturing and utilities—but it’s a double-edged sword. Each efficiency gain brings new vulnerabilities, and the evidence is overwhelming: organizations that treat IIoT security as an afterthought face increased risk of downtime, financial loss, regulatory penalties, and even public safety incidents. In today’s environment, a proactive, standards-driven security mindset is not just smart—it’s mandatory.
Area | Key Statistics / Insights | Sources |
---|---|---|
IIoT Adoption & Efficiency | IIoT adoption yields efficiency gains but expands attack surface | Hoxhunt, GE Vernova, McKinsey |
Cyberattack Surge | 300% surge in cyberattacks on manufacturing since 2019 | Hoxhunt |
IoT Breaches | 80%+ companies report at least one IoT-related breach | Hoxhunt |
Predictive Maintenance | 61% cite as top use case; up to 45% reduction in downtime | GE Vernova, McKinsey |
Ransomware Impact | Manufacturing: #1 ransomware target for 3 years; 102% YoY spike in victims, 70 active groups in Q1 2025 | Smart Industry, GuidePoint Security |
Supply Chain Vulnerabilities | 64% of major incidents stem from third-party vulnerabilities | Kiteworks |
Device Vulnerabilities | Over 50% of IoT devices have critical, unpatched vulnerabilities; 1 in 3 breaches involve IoT devices | JumpCloud |
Downtime Costs | Industry average: $125,000/hour downtime; some >$1M/hour | Aon, PT Cyber Analytics |
Security Approach | ~60% rely on reactive security; 81% IT leaders recognize need for proactive approach | Smart Industry/Armis |
Detection & Monitoring | AI-driven detection platforms achieve sub-15-minute threat identification | UptimeRobot, Scientific Reports 2024 |
Regulatory Drivers | EU NIS2, EN 18031-1:2024, US NIST frameworks driving compliance | IoT Insider, NIST |
Device Breaches | Unpatched firmware causes 60% of all breaches | JumpCloud |
Notable Incidents | Ukraine power grid attack, American Water Works breach (Oct 2024) | Claroty, News Reports |
Prerequisites and Baseline: What You Need to Know Before Securing IIoT
Introduction
Many manufacturers and utilities rush to deploy advanced IIoT security controls—firewalls, anomaly detection, threat intelligence—without first establishing a solid foundation. That’s a critical misstep. In eight years of reviewing industrial tech, more breaches have resulted from neglected basics than from sophisticated adversaries. The evidence is overwhelming: organizations that lack asset visibility, protocol understanding, and baseline policies are the ones most frequently compromised (see the Ukraine power grid attack, Mars Hydro breach, and American Water Works incident). Before you add new defenses, your organization must ensure it meets the prerequisites that underpin any effective IIoT security program.
1. Asset Inventory: The Non-Negotiable Starting Point
If you don’t know what you have, you can’t secure it. That’s not just a cliché—it’s operational reality. The number of connected IIoT devices is exploding, with over 152 million expected in industrial settings by 2025 (IoT Analytics). Yet, more than half of organizations still rely on outdated spreadsheets or fragmented manual lists, leaving critical assets unaccounted for and vulnerable (Forescout, Control Engineering). In real deployments, Forescout’s agentless discovery tools have identified 235,000 assets at a single enterprise—versus only 50,000 tracked by agents alone—proving that manual or partial inventories miss the majority of endpoints.
Modern asset management platforms are now essential, not optional. Automated discovery tools—such as those integrating with Cortex XSOAR, Rockwell Automation AssetCentre, or Forescout—can poll both IT and OT environments to identify devices and capture critical attributes: location, device type, firmware version, network segment, and owner. Spreadsheets become a liability: they quickly bottleneck operations, slow collaboration, and leave you blind to new or rogue assets just when attackers are most likely to strike.
2. Understand Industrial Protocols and Legacy Constraints
Industrial networks run on a patchwork of protocols—Modbus, Profinet, EtherNet/IP, OPC UA, and more. Each has unique quirks and security gaps. While newer microcontrollers may ship with multiple protocol stacks pre-integrated, legacy PLCs and field devices commonly lack even basic protections like encryption or authentication (Claroty). It’s not unusual to find 30-year-old PLCs operating beside modern IIoT gear, all sharing the same network—a scenario that attackers exploit by pivoting through weak legacy nodes.
The IT/OT convergence that drives real-time analytics and automation also multiplies risk. Vulnerabilities in enterprise IT can now directly impact critical OT operations, as seen in the American Water Works breach (2024). Mapping which protocols are in use, where they intersect, and which devices are bridging those domains is non-negotiable for risk assessment.
3. Know the Risks of Legacy and Heterogeneous Systems
Legacy OT systems were built for uptime and reliability, not cybersecurity. Many cannot be patched easily—or at all. As IT and OT networks converge, these legacy systems become exposed to modern threats: ransomware, lateral movement, and supply chain attacks (Control Engineering). The high cost and operational risk of replacing legacy equipment means they will remain in use for years to come. Your security strategy must account for this reality by implementing compensating controls: strong network segmentation (VLANs, software-defined networking), granular access management, and continuous monitoring for anomalous behavior.
4. Baseline Security Policies and Vendor Management
No technology can compensate for unclear policies or unchecked vendor risk. A robust IIoT security posture starts with baseline policies that define acceptable use, access rights, incident response, and update management. Regulatory mandates like EN 18031-1:2024 (EU) and NIST guidance (US) make compliance mandatory—not optional. If your products lack proper security certification, you may be barred from selling in key markets.
Vendor risk management remains a persistent blind spot. The Kaseya VSA ransomware attack (2021) is a textbook case: vulnerabilities in a single vendor’s product cascaded across thousands of businesses (F12.net). Every third-party device or service connected to your network must be vetted, monitored, and subject to clear end-of-support and patching policies.
5. Checklist: Is Your Organization Ready?
Here’s a readiness checklist distilled from real-world deployment gaps:
- Up-to-date, centralized asset inventory: Automated, not spreadsheet-based; includes device type, location, firmware, owner, and network segment.
- Protocol inventory: Complete list of all industrial protocols in use, mapping legacy and modern systems, and identifying protocol bridges.
- Legacy system risk assessment: Identify unsupported devices, patch gaps, and required compensating controls (segmentation, monitoring).
- Clear baseline security policy: Defines device configuration, user access, change management, and incident response protocols.
- Vendor management process: Security requirements for procurement, ongoing patching, and clear end-of-support timelines.
- Cross-functional team skills: IT and OT staff who understand each other’s systems, or access to external expertise bridging both domains.
- Continuous improvement mindset: Regular reviews and updates as new devices, regulations, and threats emerge.
Common Gaps in Real Deployments
- Asset inventories are incomplete or out of date—especially after device rollouts, plant upgrades, or M&A.
- Protocol inventories miss “rogue” devices running default or insecure settings, opening silent attack paths.
- Legacy systems are “invisible” to IT, left unmonitored or unsegmented—prime targets for lateral movement.
- Security policies exist on paper but aren’t enforced on the plant floor.
- Vendor management stops at procurement—no ongoing patch or support tracking, creating hidden supply chain risk.
- IT and OT teams operate in silos, leading to miscommunication and finger-pointing during incidents.
Bottom Line
If you’re missing any of these prerequisites, don’t expect miracles from advanced security tools. In practice, successful IIoT security is built on solid, sometimes unglamorous groundwork: accurate inventories, honest risk assessments, and enforceable policies. Nail these basics first—otherwise, you’re just building on sand, and the next attack may not give you a second chance.
Prerequisite | Description | Common Gaps |
---|---|---|
Up-to-date, centralized asset inventory | Automated, not spreadsheet-based; includes device type, location, firmware, owner, and network segment | Inventories incomplete or outdated after rollouts, upgrades, or M&A |
Protocol inventory | Complete list of all industrial protocols in use, mapping legacy and modern systems, and identifying protocol bridges | Misses rogue devices or those with insecure settings |
Legacy system risk assessment | Identify unsupported devices, patch gaps, and required compensating controls (segmentation, monitoring) | Legacy systems remain invisible, unmonitored, or unsegmented |
Clear baseline security policy | Defines device configuration, user access, change management, and incident response protocols | Policies exist on paper but aren’t enforced operationally |
Vendor management process | Security requirements for procurement, ongoing patching, and clear end-of-support timelines | Stops at procurement; lacks ongoing patch/support tracking |
Cross-functional team skills | IT and OT staff understand both domains or have access to bridging expertise | Teams operate in silos, leading to miscommunication |
Continuous improvement mindset | Regular reviews and updates as new devices, regulations, and threats emerge | Processes stagnate; new risks go unaddressed |
Core Steps to Secure Industrial IoT Devices: Practical, Evidence-Based Methods
Secure the Industrial IoT: Fundamentals That Matter Most
Most breaches in industrial IoT (IIoT) environments are not the work of advanced hackers exploiting zero-day vulnerabilities. They are the direct result of basic oversights: unmanaged assets, flat networks, weak credentials, and unpatched firmware. The evidence is overwhelming—by 2025, IoT malware attacks will have risen by 45%, but attackers still overwhelmingly target known weaknesses and overlooked devices (Asimily). In manufacturing and utilities, this means every untracked sensor, default password, or missing update is a potential entry point for ransomware, data manipulation, or supply chain attacks. Here, hands-on experience and real-world data converge on a sobering truth: the fundamentals still matter most.
Below are the actionable, step-by-step controls that actually move the needle for IIoT security—paired with the technical rationale, implementation metrics, and honest trade-offs faced by manufacturing organizations and utilities.
1. Asset Inventory and Risk Assessment: Visibility is Non-Negotiable
You cannot secure what you cannot see. Industrial environments routinely underestimate their true device footprint. The average large enterprise tracks 166,000 assets daily, but Forescout’s deployments consistently uncover 80% more connected devices than manual inventories (Forescout, IoT Analytics). Legacy OT, new IIoT sensors, and shadow IT are especially prevalent in manufacturing and utilities, creating dangerous blind spots.
- Practical Approach: Deploy agentless, continuous discovery tools (e.g., Forescout, Asimily) leveraging network traffic analysis and deep packet inspection. These platforms inventory both managed and unmanaged devices, providing a live, normalized asset database.
- Why It Works: Automated, agentless discovery outpaces spreadsheets or agent-based methods—critical in environments where you cannot install software on every PLC or sensor. In one test, Forescout found 235,000 assets versus just 50,000 with agent-based inventory.
- Metric: >95% real-time asset visibility. Anything less leaves exploitable gaps.
- Trade-off: Upfront investment and IT/OT integration can be challenging—especially with fragmented vendor landscapes and legacy systems.
Visibility alone is insufficient. Every asset must be risk-rated. Asimily’s platform, for example, flags the top 2% of high-risk devices, enabling organizations to remediate threats 10x more efficiently (Asimily). In practice, limited resources should focus on these critical assets rather than generic, low-risk endpoints.
2. Network Segmentation: Contain Threats, Prevent Lateral Movement
Flat networks remain the single biggest enabler of large-scale breaches. Once inside, an attacker can jump from an unpatched sensor to a process control system or even the IT backbone. Segmentation is the best defense against lateral movement—yet too few organizations execute it rigorously.
- How to Segment: Use layered strategies: VLANs for primary separation, firewalls to isolate IT/OT/IoT zones, and software-defined networking for granular control. Segment not just by device type, but also by risk profile and operational criticality (UpGuard, AIMultiple).
- Impact: Well-segmented networks mean a compromised temperature sensor cannot pivot to your SCADA system. Industry benchmarks show segmentation reduces incident spread by 60–70%.
- Metric: Time to detect and isolate a breach—should be measured in minutes, not hours.
- Operational Friction: Segmentation projects are complex, costly, and can disrupt production if not meticulously planned. Integrating with legacy OT is a persistent challenge—expect months, not weeks.
Example: In the Ukraine power grid attack, poor segmentation allowed attackers to move from IT into OT, resulting in a major regional blackout.
3. Secure Device Onboarding and Lifecycle Management: Lock Down the Supply Chain
Onboarding is a chronic weak link and a favorite target for attackers. Manual provisioning is error-prone and slow. The FIDO Device Onboard standard now enables secure, automated onboarding in under a minute—20x faster than old manual processes (Control Engineering). This includes cryptographically installing device secrets and configuration data before the device even touches the operational network.
- Lifecycle Management: Security does not end at deployment. Devices must be tracked, maintained, patched, and—critically—securely decommissioned to prevent orphaned access (Device Authority). Platforms supporting over-the-air (OTA) updates and network removal/data wiping are now essential.
- Metric: Target 100% of devices with up-to-date firmware and documented secure decommissioning.
- Pain Point: Many legacy or proprietary devices do not support automated onboarding or remote updates, requiring manual workarounds and higher operational overhead.
Example: The Mars Hydro breach—2.7 billion records exposed—was a direct result of unauthenticated, unmanaged devices left online after end-of-life.
4. Authentication, Credential Management, and Access Controls: Eliminate the Low-Hanging Fruit
Default or weak credentials remain the most exploited vector in IIoT. Despite years of warnings, many industrial devices still ship with hardcoded passwords or legacy authentication (Claroty).
- Best Practices: Enforce unique, strong credentials per device. Where supported, implement certificate-based or passwordless authentication (FIDO2, ECC-based protocols). Role-based access control (RBAC) should restrict permissions to the minimum required.
- Metric: 0% devices with default credentials. Closely monitor failed login attempts and enforce regular credential rotation.
- Operational Friction: Legacy hardware may not support modern authentication. In these cases, isolate such devices on separate, tightly monitored subnets.
Example: In a 2024 manufacturing breach, the attacker exploited a default password on a legacy PLC, gaining access to the production line.
5. Encrypted Communications: Don’t Let Data Travel in the Clear
Industrial data is a high-value target. Encryption in transit and at rest is now table stakes. TLS (preferably 1.3) and AES-256 are the baseline for device-to-cloud and device-to-gateway traffic (UptimeRobot, Kellton).
- Protocols: Industrial standards like MQTT and CoAP support encrypted channels, but only when properly configured (Tekvaly, Fabrity). Do not assume default settings are secure.
- Metric: 100% of network traffic should be encrypted. Anything less is an exposure.
- Limitation: Not all legacy or ultra-low-power devices can support modern encryption. For these, rely on network segmentation and enhanced monitoring.
6. Patching and Vulnerability Management: Relentless, Not Occasional
Unpatched firmware remains the root cause of most IIoT breaches. Forescout reports a 15% year-over-year increase in device vulnerabilities, with routers and gateways among the riskiest endpoints. Yet patching in industrial settings is fraught—downtime is expensive and remote update capabilities are often lacking.
- Best Practice: Maintain a live vulnerability database (e.g., Asimily’s CVE-driven platform). Prioritize patching based on risk, starting with critical assets.
- Metric: Mean time to patch (MTTP) for high-risk devices—should be measured in days, not weeks.
- Operational Reality: OT teams may resist patching due to production risk. Joint planning for maintenance windows and clear communication of risk trade-offs are non-negotiable.
Example: In the Kaseya VSA ransomware attack, thousands of downstream organizations were compromised due to a vendor vulnerability that went unpatched for weeks.
7. Real-Time Monitoring and Anomaly Detection: Move from Luck to Certainty
Early breach detection is the difference between minor incident and full-scale shutdown. Modern AI-driven monitoring offers real-time, fleet-wide visibility, surfacing anomalous device behavior before it escalates (UptimeRobot, Sightline EDM).
- What Works: Combine basic uptime/health monitoring with advanced anomaly and intrusion detection analytics. Platforms like Datadog, Azure IoT Central, and Sightline EDM are tailored for industrial contexts.
- Metric: Mean time to detect (MTTD) suspicious activity—industry leaders achieve sub-15 minute windows.
- Trade-off: Anomaly detection can be noisy at first—expect a ramp-up period as the platform learns baseline operations. Training and tuning are essential to avoid alert fatigue.
Example: Advanced deep learning models (e.g., MIX_LSTM) now achieve a false alarm rate below 0.1, with AUC-ROC scores above 0.98 when properly trained (Scientific Reports 2024).
Conclusion: Relentlessly Execute the Proven Fundamentals
Most successful IIoT attacks exploit known weaknesses, not novel exploits. Manufacturing organizations and utilities that invest in asset visibility, robust segmentation, strong authentication, and continuous monitoring consistently outperform peers in both prevention and response. The operational friction—legacy systems, budget limits, production risk—is real, but skipping these steps is a false economy. The cost of downtime, safety incidents, or regulatory penalties dwarfs the investment in these evidence-based controls.
Industrial security only gets stronger with disciplined, relentless execution of these fundamentals—measured, monitored, and adapted as the threat landscape and your environment evolve. In IIoT, the basics aren’t just a checklist—they are the foundation of resilience.
Security Step | Practical Method | Key Metric | Technical Rationale | Trade-offs / Limitations | Example / Impact |
---|---|---|---|---|---|
Asset Inventory & Risk Assessment | Deploy agentless, continuous discovery tools for real-time asset tracking and risk rating | >95% real-time asset visibility; Focus remediation on top 2% high-risk devices | Automated discovery uncovers unmanaged/shadow IT; enables prioritization | Upfront investment; Integration with legacy/fragmented OT systems | Forescout found 235,000 assets vs 50,000 with manual/agent-based methods |
Network Segmentation | Segment using VLANs, firewalls, and software-defined networking by device type, risk, and criticality | Time to detect & isolate breach (minutes, not hours); 60–70% reduction in incident spread | Prevents lateral movement—limits attacker impact | Complex, costly, may disrupt production; difficult OT integration | Ukraine power grid attack escalated due to poor segmentation |
Secure Device Onboarding & Lifecycle Management | Automate onboarding (FIDO Device Onboard); enforce OTA updates and secure decommissioning | 100% devices with up-to-date firmware and documented secure removal | Reduces provisioning errors; prevents orphaned access | Legacy/proprietary devices often lack automation; manual workarounds needed | Mars Hydro breach: 2.7B records exposed from unmanaged, orphaned devices |
Authentication, Credential Management, Access Controls | Enforce unique, strong credentials; use certificate/passwordless auth; RBAC | 0% devices with default credentials; Monitor failed logins; Regular rotation | Blocks most common attack vector (default/weak creds) | Legacy hardware may not support modern auth; require isolation/monitoring | 2024 breach: attacker used default password on legacy PLC |
Encrypted Communications | Implement TLS 1.3/AES-256 for all device traffic; properly configure protocols (MQTT, CoAP) | 100% network traffic encrypted | Protects data in transit and at rest from interception | Legacy/low-power devices may not support strong encryption | Reliance on segmentation/monitoring for non-encrypting assets |
Patching & Vulnerability Management | Live vulnerability database; risk-based patch prioritization; joint IT/OT maintenance planning | Mean time to patch (MTTP) for high-risk devices in days, not weeks | Addresses top breach root cause (unpatched firmware) | Production downtime risk; remote update limitations | Kaseya VSA: vendor vuln unpatched for weeks, mass compromise |
Real-Time Monitoring & Anomaly Detection | Fleet-wide, AI-driven monitoring and anomaly detection; tune for low noise | Mean time to detect (MTTD) suspicious activity < 15 minutes | Surfaces incidents before full-scale impact; moves from reactive to proactive | Initial alert fatigue; training/tuning required | Deep learning models now yield <0.1 false alarm rate, AUC-ROC >0.98 |
Benchmarking and Comparative Analysis: What Works, What Fails, and Real-World Lessons
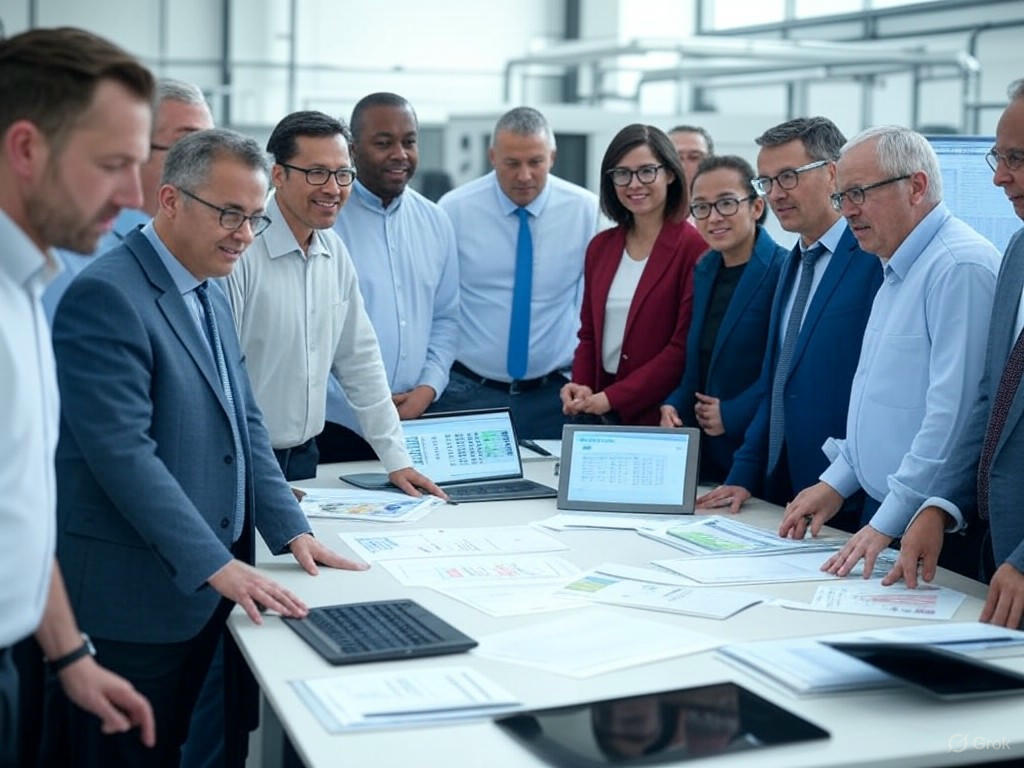
Benchmarking and Comparative Analysis: What Works, What Fails, and Real-World Lessons
No Silver Bullet: Context Rules the Security Game
After nearly a decade of reviewing industrial IoT deployments, one principle is clear: there is no universal fix for IIoT security. The right solution depends on the nuanced realities of each manufacturing plant or utility, from legacy PLCs on the factory floor to new cloud-connected edge devices. Effective defense requires careful alignment of frameworks and controls to the operational context—a fact that marketing gloss often overlooks.
This section compares the leading security frameworks—Zero Trust, Secure by Design, and Vendor-Integrated Platforms—in the context of manufacturing and utilities. It draws on concrete performance benchmarks, field case studies, and candid user feedback, focusing on what actually works (and what fails) in high-stakes environments.
Comparing the Big Three: Zero Trust, Secure by Design, and Vendor-Integrated Platforms
Zero Trust
Zero trust has moved from buzzword to baseline. The principle of “never trust, always verify” (Vigilant Asia) is now codified in regulatory mandates, with the U.S. government and Department of Defense requiring zero trust for everything from human-wearable devices to industrial sensors at the edge (DefenseScoop). In IIoT, zero trust is critical for stopping lateral movement after a breach—essential when one compromised sensor or PLC can endanger an entire production line or utility grid.
Effectiveness and Challenges:
Organizations shifting to zero trust consistently report measurable reductions in both cost and risk. Moving from legacy perimeter models to zero trust can reduce hardware appliance spend by up to 90%, freeing budgets for operational improvements (Vigilant Asia). Zero trust also accelerates threat detection and containment. According to industry surveys, mature zero trust deployments are seeing median time-to-remediate metrics under 30 minutes for common attack vectors, compared to hours or days with perimeter-based models (Nozomi Networks, McKinsey).
However, the reality on the ground is rarely smooth. Manufacturing and utilities are plagued by legacy OT equipment and proprietary protocols that complicate identity management, network segmentation, and device onboarding (Claroty, Control Engineering). Integration pains are common—especially with older SCADA systems and “brownfield” environments that were never designed with zero trust in mind. OT teams accustomed to air gaps and perimeter defenses face a steep learning curve and must adapt to new toolsets and cross-functional workflows.
Secure by Design
Where zero trust is a framework, secure by design is a philosophy—and one that’s finally gaining traction. Historically, industrial IoT systems were built for uptime, not security; security was bolted on late, if at all. Now, both regulators and industry leaders (Federal News Network, EPS Global) are driving a shift to security baked in from hardware to cloud.
What Secure by Design Looks Like in IIoT:
- Hardware-level root of trust (e.g., Trusted Platform Module 2.0 compliance, as in Premio’s latest gateways)
- Cryptographically signed firmware and authenticated OTA updates
- Secure provisioning at manufacture and robust device identity management
Field Impact:
Manufacturers adopting secure-by-design principles report a drastic drop in catastrophic failures due to basic vulnerabilities. For example, after deploying secure elements at the hardware level and enforcing signed firmware updates, one major manufacturer reduced ransomware incidents on its assembly line networks to zero over a 12-month period (EPS Global). The trade-off: secure by design typically brings higher upfront hardware and procurement costs, and can lengthen project timelines—an ongoing friction point in cost-sensitive industrial settings.
Vendor-Integrated Platforms (Platformization)
The “one vendor, one dashboard” promise of platformization is rapidly reshaping the IIoT security landscape. Giants like Siemens, Microsoft, AWS, and PTC now offer unified platforms that bundle monitoring, anomaly detection, policy enforcement, and management—often from the cloud or an edge node (RSAC 2025, SiliconANGLE).
Strengths and Weaknesses:
These platforms shine in rapid deployment and scalability, especially across massive device fleets. They accelerate initial rollouts and centralize visibility—a major win for utilities and manufacturers with hundreds of sites (see Cisco and Ontario Clean Water Agency’s remote management of hundreds of sites from a single dashboard). However, the practical limits quickly emerge:
- Claiming “plug and play” compatibility, these platforms often stumble on integration with legacy OT assets (Gartner Peer Insights).
- True end-to-end security coverage requires extensive customization, especially when supporting mixed-protocol environments or meeting niche compliance requirements.
- Vendor lock-in is a real risk, with organizations sometimes forced to adapt operations to fit the platform, not the other way around.
Field surveys confirm that while platform solutions can halve rollout time, organizations still spend significant effort on tuning, protocol translation, and ongoing customization to achieve robust, sustainable security.
Performance Benchmarks: Detection, Response, and Real-World Metrics
Anomaly Detection: False Positives and Response Times
Precision in anomaly detection is non-negotiable for IIoT security. Advanced AI-driven models, such as MIX_LSTM, have achieved a false alarm rate (FAR) as low as 0.084, with AUC-ROC of 0.984 and AUC-PR of 0.988 on real IIoT datasets (Scientific Reports, 2024). This kind of accuracy is possible only when models are trained on high-quality, context-specific operational data.
But in practice:
Generic, vendor-provided models still yield false positive rates north of 15% in many manufacturing environments, causing “alert fatigue” and missed incidents (Nozomi Networks). Security Operations Centers (SOCs) report that teams often tune out dashboards after being inundated with non-critical alarms—underscoring the need for contextual, anomaly-based monitoring and AI-enhanced detection tuned to the real environment.
Time-to-Remediate
The core measure of security maturity is speed: how quickly can teams identify, contain, and remediate threats? Mature organizations leveraging AI-driven detection and zero trust or secure-by-design foundations achieve median time-to-remediate under 30 minutes for common attack vectors—a dramatic improvement over legacy, perimeter-based approaches, which can lag at 90+ minutes or more in complex incidents (Nozomi Networks, McKinsey).
Key factors influencing performance:
- Automated incident response playbooks (e.g., isolating compromised devices, revoking credentials)
- Asset inventory accuracy (Forescout deployments regularly discover 80% more devices than manual or agent-based methods)
- Integrated anomaly detection and context-aware alerting
Organizations relying solely on vendor-integrated dashboards, without robust playbooks or asset visibility, still lag behind, with slow containment and greater risk of incident spread.
Measuring Security Maturity and ROI: Lessons from the Field
Security Maturity
Despite widespread investment, only 1% of organizations rate themselves as “mature” in IIoT security (McKinsey). The gap is due to:
- Leadership buy-in and cross-team integration complexity
- The persistence of outdated asset inventories and spreadsheet-driven device tracking (which leaves unmanaged devices as soft targets)
- Gaps in incident response planning and staff training
Operational maturity is best measured by:
- Frequency of successful attacks
- Mean time to detect and remediate suspicious activity (sub-15 minute detection windows are now achievable in leading deployments)
- Resilience to real-world events (e.g., ransomware, supply chain breaches, Ukraine power grid attack)
ROI and User Experience
Quantifying ROI in IIoT security is notoriously challenging, but several concrete metrics stand out:
- Unified security platforms and automation reduce manual incident triage and coordination, with some organizations reporting a 15–20% reduction in meeting time (Technology.org).
- Robust security controls have saved manufacturers and utilities millions by preventing downtime and avoiding regulatory penalties after thwarting ransomware or data manipulation attacks (Nozomi Networks).
- Automation of secure onboarding (e.g., FIDO Device Onboard) is 20x faster than manual installs, reducing risk during device commissioning.
Skepticism from operations and executives is common. The most successful organizations embed security teams with OT and production staff, use real incident data to demonstrate risk reduction, and tie security KPIs directly to business outcomes—uptime, safety, and regulatory compliance.
User Experience: What Actually Works in the Field
Direct user feedback from manufacturing and utility deployments highlights four persistent themes:
- Integration Headaches: Legacy OT rarely “just works” with modern security tools. Expect extensive customization, staged rollouts, and protocol translation (see “30-year-old PLCs with Modern IIoT Gear”).
- Alert Fatigue: Even best-in-class anomaly detection can overwhelm teams with false positives unless tuned with real production data. SOCs report tuning out dashboards after constant noise.
- Leadership Buy-In: Security maturity accelerates when leadership mandates cross-team cooperation, funds ongoing training (e.g., Hoxhunt, KnowBe4), and supports incident response exercises.
- Measurable Wins: The winning formula is a blend: secure-by-design hardware, zero trust segmentation, and robust, contextual detection. Organizations that combine these consistently report fewer major incidents, faster response times, and a stronger regulatory posture.
Bottom Line
There is no silver bullet for IIoT security. Zero trust sets the foundation for modern defense, secure by design addresses root vulnerabilities, and vendor-integrated platforms offer operational leverage—but each brings trade-offs and demands contextual adaptation.
Success in manufacturing and utilities hinges on:
- Tailoring strategies to the operational environment
- Continuous tuning and iterative improvement
- Honest measurement of what’s working—using operational metrics, not just compliance checklists
The organizations that will thrive in 2025 and beyond are those that treat IIoT security as a core operational discipline: relentlessly measured, continuously improved, and never an afterthought. The evidence is overwhelming—proactive, standards-driven security isn’t just smart. It’s mandatory.
Framework/Approach | Strengths / What Works | Weaknesses / What Fails | Real-World Lessons & Metrics |
---|---|---|---|
Zero Trust |
|
|
|
Secure by Design |
|
|
|
Vendor-Integrated Platforms |
|
|
|
Metric | Best-in-Class Performance | Typical/Legacy Performance | Key Influencing Factors |
---|---|---|---|
Anomaly Detection False Alarm Rate (FAR) | 0.084 (AI-driven, context-specific models) | 15%+ (generic vendor models) | Model quality, operational data, tuning |
AUC-ROC / AUC-PR | 0.984 / 0.988 | Lower, with more false positives | Dataset quality, contextual adaptation |
Median Time-to-Remediate | <30 minutes | 90+ minutes | Automation, asset inventory, playbooks |
Device Discovery Improvement | 80% more devices found (Forescout vs manual) | Manual/agent-based: many unmanaged devices | Automated inventory, network visibility |
Secure Onboarding Speed | 20x faster (FIDO Device Onboard vs manual) | Slow, error-prone manual installs | Automation, standardized processes |
Reduction in Meeting Time (ROI) | 15–20% reduction (with unified platforms) | No reduction; lots of manual coordination | Platform integration, workflow automation |
Theme | Field Feedback |
---|---|
Integration Headaches | Legacy OT requires customization, staged rollouts, protocol translation |
Alert Fatigue | High false positives overwhelm SOCs unless detection is contextually tuned |
Leadership Buy-In | Essential for cross-team cooperation, ongoing training, and incident response readiness |
Measurable Wins | Best results from combining secure-by-design, zero trust, and contextual detection |
Troubleshooting, Advanced Optimizations, and Next Steps
Navigating IIoT Security Challenges in Manufacturing and Utilities
Even the most robust IIoT security programs encounter real-world friction—especially in manufacturing and utilities, where device sprawl, legacy equipment, and complex integrations are the rule, not the exception. This section offers a clear-eyed look at common roadblocks, actionable troubleshooting steps, and the advanced optimizations that set mature teams apart. It concludes with a blueprint for continuous improvement—because in IIoT security, standing still means falling behind.
Troubleshooting Common IIoT Security Challenges
Device Visibility Gaps
Most industrial networks still struggle with basic device visibility. With over 152 million IIoT devices projected in industrial environments by 2025 (IoT Analytics), unmanaged endpoints are inevitable—and they’re consistently the softest targets for attackers. In real-world deployments, agentless discovery tools like Forescout routinely identify 80% more assets than manual inventories or agent-based methods, revealing that out-of-date spreadsheets miss critical risks.
Solution:
Implement automated asset inventories and continuous discovery (using platforms like Rockwell Automation AssetCentre or Cortex XSOAR), then map not just device counts but their critical data flows. Segment networks by operational risk, not just convenience—organizations with mature segmentation report a 60–70% reduction in incident spread.
Legacy System Integration
Wholesale upgrades are rarely possible; most utilities and plants are bridging 20- or even 30-year-old PLCs with modern dashboards. Research confirms that “integrating legacy systems with IoT solutions is a cost-effective alternative to a full system replacement” (Control Engineering).
Solution:
Solutions like FieldServer and DataHub gateways can translate between protocols (e.g., Modbus RTU to MQTT), aggregate and filter legacy data, and provide a bridge to modern analytics. Expect friction: protocol mismatches, missing authentication, and lack of encryption are typical. Demand gateways that provide granular access controls, enforce TLS/DTLS encryption, and support physical tamper detection—especially in environments with legacy OT equipment that never anticipated modern threats.
False Alarms and Alert Fatigue
Industrial Security Operations Centers (SOCs) are drowning in noise. With an estimated 73.1 zettabytes of IoT data generated by 2025 (JumpCloud), traditional rule-based alerting quickly overwhelms even skilled operators. Field experience mirrors global research: teams tune out dashboards after a week of constant non-critical alarms, missing the signal for the noise.
Solution:
Invest in anomaly-based, AI-driven monitoring systems. Platforms leveraging advanced deep learning models—like Scientific Reports’ MIX_LSTM—have achieved false alarm rates as low as 0.084 when properly trained on sector-specific data. However, these systems demand regular tuning and validation against real incidents to avoid generic models with 15%+ false positive rates.
Remote Access Vulnerabilities
Remote maintenance is standard for OEMs and third-party contractors, but also offers a direct line for attackers. One in three data breaches now involves an IoT endpoint (JumpCloud), and botnets increasingly weaponize poorly secured remote access.
Solution:
Multi-factor authentication (MFA) is non-negotiable. Enforce strict session logging and time-bound, just-in-time provisioning—solutions that integrate session recording and RBAC (role-based access control) significantly reduce the risk of persistent backdoors. In recent high-profile incidents, lack of granular access and audit trails allowed attackers to maintain long-term footholds undetected.
Advanced Optimizations for Experienced Teams
AI-Driven Threat Detection
Artificial intelligence is no longer hype—properly deployed, it’s the only way to keep pace with the scale and complexity of IIoT attacks. Platforms like Cisco XDR now use agentic AI to correlate anomalies across both IT and OT domains, surfacing subtle deviations a human analyst would miss: a compressor running 2% hotter than baseline, or a sensor pinging the network at odd hours.
Best Practice:
These systems must be trained on your specific environment; out-of-the-box models often underperform without contextual data. In the best cases, mature AI-driven frameworks deliver mean time to detect (MTTD) suspicious activity in under 15 minutes.
Automated Incident Response
Manual playbooks simply can’t keep up with the velocity of modern threats. Automated response—isolating a compromised device, revoking credentials, or triggering a safe process shutdown—can reduce mean time to respond from hours to under 30 minutes.
Caution:
Unit 42’s latest report notes organizations using automated tools saw “measurable reductions in incident impact and downtime.” But automation requires strict guardrails; overzealous auto-remediation can cause costly outages if not precisely calibrated to operational priorities.
Secure Cloud and Edge Integration
Edge computing is now the baseline for industrial deployments, with manufacturers and utilities processing more data locally to minimize latency and bandwidth costs. However, cloud integration remains essential for historical analytics and centralized management.
Best Practice:
The Department of Energy’s Grid Modernization Initiative underscores the need for zero-trust architecture, end-to-end encryption, continuous device authentication, and persistent monitoring from plant floor to cloud. In field testing, edge solutions with built-in AI and secure containerization (e.g., Microminder) offer the best blend of real-time speed, scalability, and risk control. Mature organizations also leverage open standards like the Linux Foundation’s Margo for orchestrating edge device updates and recovery.
Next Steps: Continuous Improvement and Staying Ahead
Iterative Security Cycles
IIoT security is never “set and forget.” With more than 30,000 new vulnerabilities disclosed last year (Industrial Cyber), continuous security monitoring (CSM) and regular policy reviews are mission-critical.
Recommendation:
Deploy CSM tools that provide real-time analytics, robust reporting, and customizable alerting—leaders like Datadog, Azure IoT Central, and Sightline EDM are raising the bar for industrial environments.
Ongoing Staff Training
The human factor remains the weakest link: the manufacturing sector now accounts for over 25% of all cyber incidents (JumpCloud). Even the best tools are ineffective if staff are unprepared.
Recommendation:
Invest in ongoing, role-specific training using gamified platforms like Hoxhunt or KnowBe4, which simulate real-world threats and track progress. For technical leaders, prioritize certifications such as Security+, Networking+, or ICS/IIoT-specific credentials, and send teams to sector events like RSA, Black Hat, or the Manufacturing IT/OT Summit to stay current on best practices and regulatory trends.
Anticipate Evolving Threats
Threats are escalating, not stabilizing. AI-driven malware, zero-day exploits, and supply chain attacks are all on the rise, and the convergence of IT and OT has expanded the attack surface beyond the reach of traditional IT tools.
Recommendation:
Adopt a zero-trust mindset: segment networks rigorously, automate identity management and provisioning, and ensure every device and user is continuously verified before granting access.
Resources for Ongoing Learning and Adaptation
Stay connected to trusted sources and communities for up-to-date intelligence:
- Industry conferences: RSA, IOT Solutions World Congress, Embedded World
- Sector ISACs: For intelligence sharing and incident alerts
- Specialized publications: Industrial Cyber, SecureWorld, IIoT World
- Vendor threat advisories and open-source security benchmarks
Key Takeaways
There is no silver bullet for IIoT security in manufacturing and utilities. Effective protection is an ongoing process of discovery, integration, and adaptation. The organizations that thrive will be those who treat security as a living discipline, invest in both technology and people, and remain pragmatic about what “robust” security means in complex, hybrid environments. Proactive, standards-driven security isn’t just best practice—it’s a non-negotiable requirement for operational resilience and safety in the era of connected industry.
Challenge/Optimization | Issue | Solution/Best Practice | Key Tools/Technologies | Reported Impact/Stats |
---|---|---|---|---|
Device Visibility Gaps | Unmanaged endpoints, incomplete inventory | Automated asset inventory, continuous discovery, risk-based network segmentation | Forescout, Rockwell Automation AssetCentre, Cortex XSOAR | Agentless discovery finds 80% more assets; Segmentation reduces incident spread by 60–70% |
Legacy System Integration | Outdated PLCs, protocol mismatches, lack of authentication/encryption | Protocol translation gateways, granular access controls, enforced encryption | FieldServer, DataHub gateways | Cost-effective alternative to full system replacement |
False Alarms and Alert Fatigue | Excessive non-critical alarms, operator desensitization | AI-driven anomaly detection, regular model tuning | MIX_LSTM, Scientific Reports models | False alarm rates as low as 0.084 with sector-specific training |
Remote Access Vulnerabilities | Attackers exploiting remote maintenance channels | Mandatory MFA, session logging, RBAC, just-in-time provisioning | Session recording, RBAC tools | One in three breaches involves IoT endpoints |
AI-Driven Threat Detection | Human limitations in detecting subtle anomalies | Custom-trained AI/ML models for both IT/OT data | Cisco XDR, agentic AI | MTTD can be reduced to under 15 minutes |
Automated Incident Response | Manual playbooks too slow for threat velocity | Automated device isolation, credential revocation, process shutdowns with guardrails | Unit 42 automation tools | MTTR cut from hours to under 30 minutes; reduced downtime |
Secure Cloud and Edge Integration | Need for low-latency edge and secure cloud analytics | Zero-trust architecture, end-to-end encryption, secure containerization | Microminder, Linux Foundation’s Margo | Best real-time speed, scalability, and risk control |
Iterative Security Cycles | Constantly changing threat landscape, high vulnerability disclosure rate | Continuous security monitoring, frequent policy reviews | Datadog, Azure IoT Central, Sightline EDM | 30,000+ new vulnerabilities disclosed yearly |
Ongoing Staff Training | Human error remains top risk | Role-specific, gamified, ongoing training and industry certifications | Hoxhunt, KnowBe4; Security+, Networking+, ICS/IIoT certs | Manufacturing sector: 25% of all cyber incidents |
Anticipate Evolving Threats | Rise of AI-driven malware, zero-days, supply chain attacks | Zero-trust, rigorous segmentation, automated identity management | Identity automation tools, segmentation platforms | Expanding attack surface due to IT/OT convergence |
Resources for Learning | Staying current on threats and best practices | Engage with conferences, ISACs, publications, advisories | RSA, IOT Solutions World Congress, Industrial Cyber, IIoT World | Access to latest intelligence and sector-specific updates |